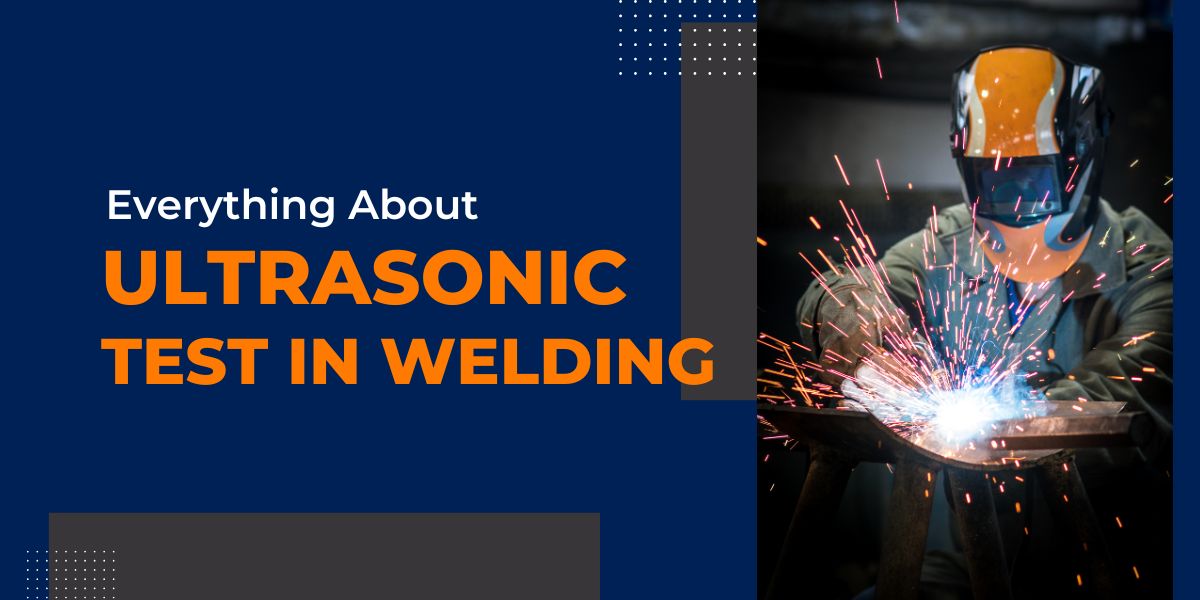
Ultrasonic Testing (UT) is a foundation of modern non-destructive testing (NDT) techniques, particularly in welding. It allows one to inspect for internal defects and discontinuities within welds without going through a destructive process, maintaining the component’s structural integrity and safety throughout industries like construction, manufacturing, oil and gas, and aerospace. In this blog, we will discuss everything about ultrasonic test in welding, from what it is and how it works to its benefits and applications.
What Is Ultrasonic Testing?
Ultrasonic Testing is a non-destructive inspection technique that uses high-frequency sound waves, typically above 20,000 Hz (20 kHz), to evaluate the internal structure of materials and weld joints. In welding, UT is mostly used to identify and characterise defects like cracks, porosity, slag inclusions, lack of fusion, and other discontinuities that can weaken the strength and longevity of a welded joint.
This method is versatile and can be used on a broad variety of materials such as metals, plastics, composites, and ceramics. It is particularly useful where the surface seems perfect but there might be hidden flaws that would cause catastrophic failures if not detected.
How Ultrasonic Test in Welding Works
Ultrasonic testing operates on the principle of introducing high-frequency sound waves through a material and analysing their interaction with internal features. It requires the following:
- Transducer: The core of UT equipment, the transducer (or probe) has a piezoelectric crystal that translates electrical pulses into ultrasonic waves and vice versa.
- Couplant: It is a gel or liquid that is applied between the transducer and the test surface to facilitate efficient transmission of sound waves into the material.
- Pulser/Receiver: The electronic unit that supplies electrical pulses for the transducer and receives the reflected signals.
- Display Unit: Visualises the received signals, usually as a digital or waveform display, for interpretation of the data.
Testing Procedure
- Surface Preparation: The weld and surrounding area are cleaned to ensure good contact between the transducer and the material.
- Couplant Application: Couplant is applied to remove air gaps that may hinder the flow of sound waves.
- Transducer Placement: The transducer is placed on the surface, and ultrasonic waves are introduced into the weld.
- Wave Propagation and Reflection: As the sound waves pass through the weld, they reach boundaries or defects. Some of these waves are reflected back to the transducer.
- Data Acquisition: The reflected waves are picked up by the transducer, reconverted into electrical signals, and presented for analysis.
- Analysis: The signals are read by technicians, and the time of flight and amplitude are measured to establish the size, position, and type of any discontinuity.
Modes of Ultrasonic Testing
- Pulse-Echo (Reflection): Here the same transducer sends and receives pulses. Reflections from flaws or the back wall are analysed to detect and locate defects.
- Through-Transmission (Attenuation): Here one transducer sends, and another receives. A reduction in signal strength indicates the presence of internal flaws.
Advanced Techniques
Modern UT includes phased array and time-of-flight diffraction (TOFD), which provide real-time imaging and more detailed characterisation of weld defects.
Benefits of Ultrasonic Testing
Ultrasonic test in welding offers the following advantages that make it the preferred choice for weld inspection in many industries:
- Non-Destructive: The test does not damage or alter the component, allowing for continued use after inspection.
- High Accuracy and Sensitivity: It can detect very minor defects well within the material, which other NDT methods often fail to detect.
- Quantitative Measurement: Itdelivers the exact details regarding defect size, position, and direction, supporting proper evaluation and repair planning.
- Versatility: It is suitable for testing a wide variety of materials and geometries, including complex weld joints, pipes, plates, and castings.
- Speed and Efficiency: UT can be conducted quickly, minimising downtime and increasing productivity.
- Real-Time Results: It offers immediate feedback, which allows for rapid decision-making and corrective actions.
- Cost-Effective: It eliminates the need for destructive methods for testing, reducing material wastage and associated costs.
- Minimal Access Needed: Testing of a component using this method usually requires access to only one side, which is ideal for in-situ inspections.
- Portability: New UT equipment is lightweight and portable, which allows on-site inspections in challenging environments.
Ultrasonic Test in Welding: Practical Applications
In welding, ultrasonic testing is indispensable for:
- Ensuring weld quality and integrity of critical structures like bridges, pipelines, pressure vessels
- Identification of hidden flaws that may result in failure under fatigue or stress
- Checking for compliance with the industry norms and safety specifications
- Detecting early-stage defects before they become a serious problem
Common weld defects detected by UT include:
- Porosity
- Cracks (surface and subsurface)
- Slag inclusions
- Lack of fusion or penetration
- Root concavity
- Crater pipes
- Undercuts and burn-throughs
Ultrasonic testing is a strong, consistent, and effective technique for weld inspection. Its ability to detect very small internal flaws and provide quantitative data without harming the component makes it of tremendous value in safeguarding safety and quality in any industry. With technology advancing day by day, ultrasonic testing continues to find new means of becoming more accurate and incorporating real-time imaging, making it all the more indispensable as a tool in welding and other applications.
Trust Gammax Independent Inspection Services for Expert Ultrasonic Testing Services
Here at Gammax Independent Inspection Services Ltd, we provide ultrasonic testing (UT) services to verify the integrity and quality of welds for any industry. Accredited to ISO 17020 and ISO 17024, we use certified personnel and state-of-the-art manual contact techniques for ultrasonic flaw detection and thickness measurement.
Our services allow for prompt detection of internal weld defects accurately that enables compliance with client requirements and safety codes. Having experience in civil engineering and steel fabrication work, we provide fast response, effective inspection, and transparent reporting that makes us a trusted partner for weld testing and certification. Call us today for ultrasonic testing or any other non-destructive welding inspection services.