Dye Penetration Test
Your search for the most reliable dye penetration test service provider in the UK ends here!
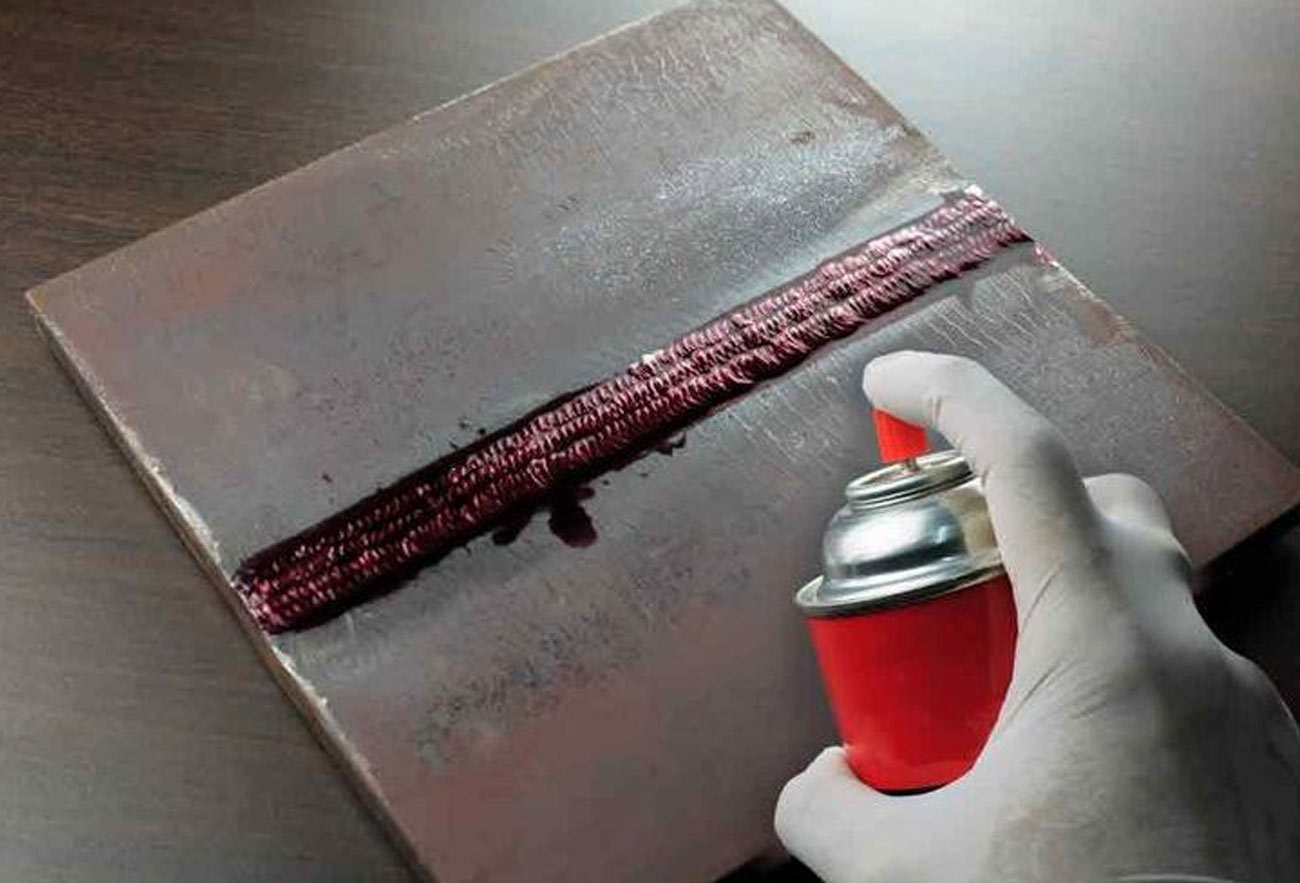
Welcome to Gammax Independent Inspection Services Ltd – your go-to specialist in Non-Destructive Testing (NDT) methods since 1995. We serve a large number of clients in a variety of sectors, only offering high-quality services.
A dye penetration test falls under the Liquid Penetrant Inspection (LPI) category among NDT techniques to find imperfections in metal welds.
Liquid penetrant testing, while recognised as having lower sensitivity than magnet particle testing for ferritic objects, is still highly sensitive and straightforward in detecting surface-breaking defects. It also offers the advantage of applying to all nonporous materials.
Furthermore, it has a wide range of surface temperature suitability (10-50 C) and requires meticulous surface cleanliness, ensuring accurate and reliable results. These considerations make it an effective and versatile testing method for flaw detection in various industries.
Our Services
We test welds so that you don’t have to
- GIIS Ltd, Units 12-13, Oaklands Business Park, Bury St Edmunds, Suffolk, IP33 2RW
- 01284 850 888
- info@gammax.co.uk
What is a dye penetration test?
The dye penetration test, also known as liquid penetrant inspection (LPI) or dye penetrant inspection (DPI), is a non-destructive testing method used to detect surface defects or cracks in materials, particularly metals.
It involves applying a liquid dye to the material’s surface, allowing it to seep into any surface cracks or flaws through capillary action. After a specified time, the excess dye is removed, and a developer is applied to draw out the trapped dye.
The dye penetrant test helps reveal defects that may not be visible to the naked eye, enabling further evaluation and necessary repairs.
Why is the dye penetration test important in the metal industry?
The dye penetration test plays a crucial role in the metal industry for quality control and ensuring the integrity of metal components. Identifying surface cracks, fractures, or other defects prevents potential failures, ensuring the structural soundness of metal parts. This test aids in detecting manufacturing flaws, material inconsistencies, or damage caused during the fabrication, welding, or handling processes.
Early detection of defects through the dye penetration test allows for timely repairs or replacements, preventing costly and hazardous consequences, such as equipment failure, structural collapse, or compromised safety. Overall, it helps maintain the high standards of quality and reliability expected in the metal industry.
Benefits of dye penetration test over other NDT methods
- Instant results: The dye penetration test provides immediate visual results, allowing for prompt identification of surface defects or cracks – enabling quick decision-making.
- Cost-effective: Dye penetration testing is relatively inexpensive compared to other non-destructive testing methods. The cost-effective solution for detecting surface flaws also minimises the need for expensive repairs or replacements down the line.
- On-site inspection: The test can be conducted on-site, eliminating the need to transport materials or components to a testing facility. This convenience saves time and ensures an efficient inspection process.
- Water and solvent removable: Dye penetrants used in the test are typically water or solvent-based, making them easy to remove after the inspection. This allows for a clean and residue-free surface, reducing post-testing cleanup efforts.
- V. Dip Tank System: We provide a U.V. dip tank system, which enhances the dye penetration process by utilising ultraviolet light to improve visibility and defect detection. This technology increases the accuracy and reliability of the test results.
Gammax is the best option if you need welding procedures or certifications that adhere to BS EN 15614, BS EN ISO 9606, or ASME IX. We can offer guidance on the diameter and thickness of pipes and plates to be used for maximum qualification.
Need some advice? Or want to book in?
Unlock precision and peace of mind. Call now for expert Dye Penetration Test services.
Gammax Services
Gammax Independent Inspection Services Ltd is the leading Non Destructive
Testing Specialist
Services
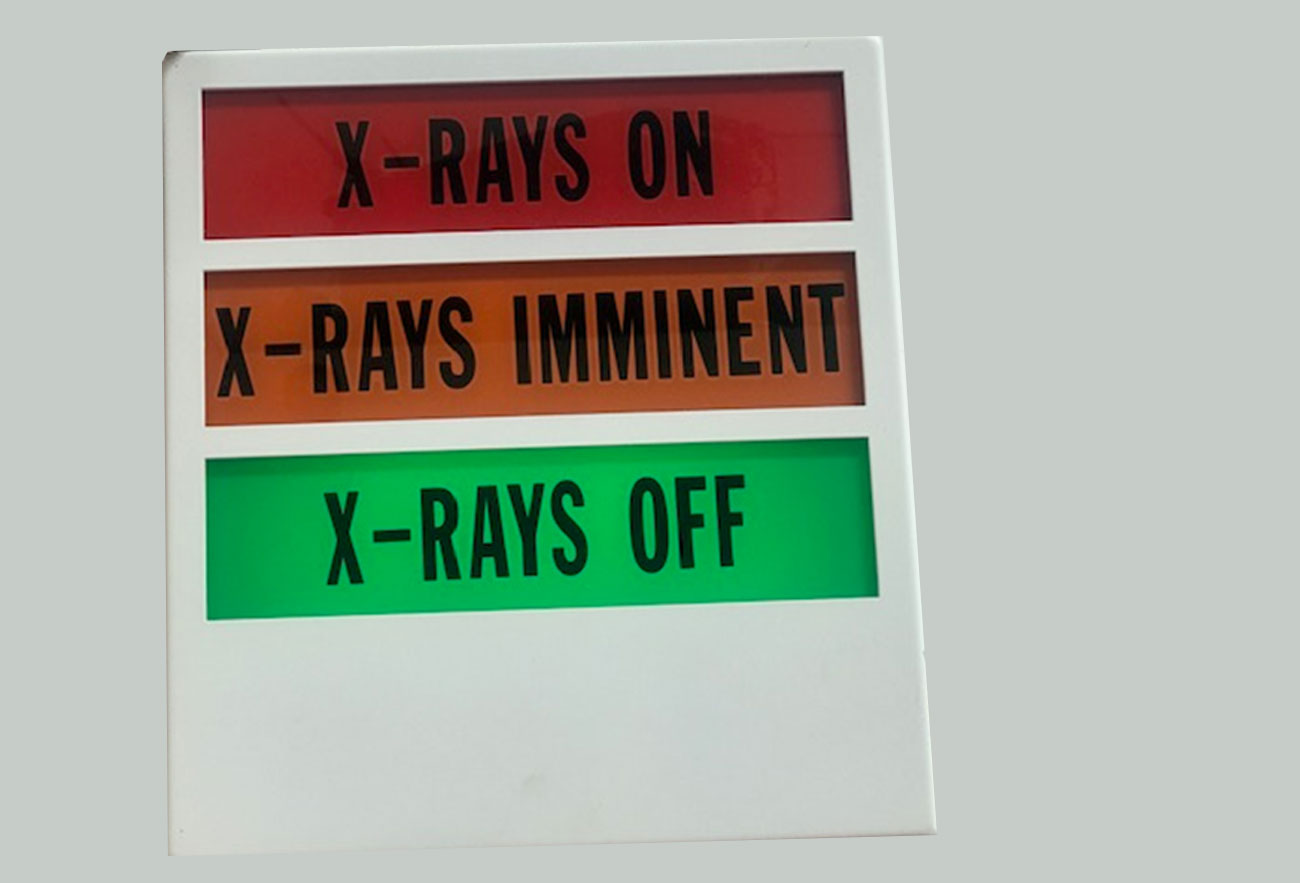
Radiography
Radiography utilises penetrating radiation generated electrically by x-ray equipment or by the nuclear decay process seen in radioactive isotopes such as Iridium 192.
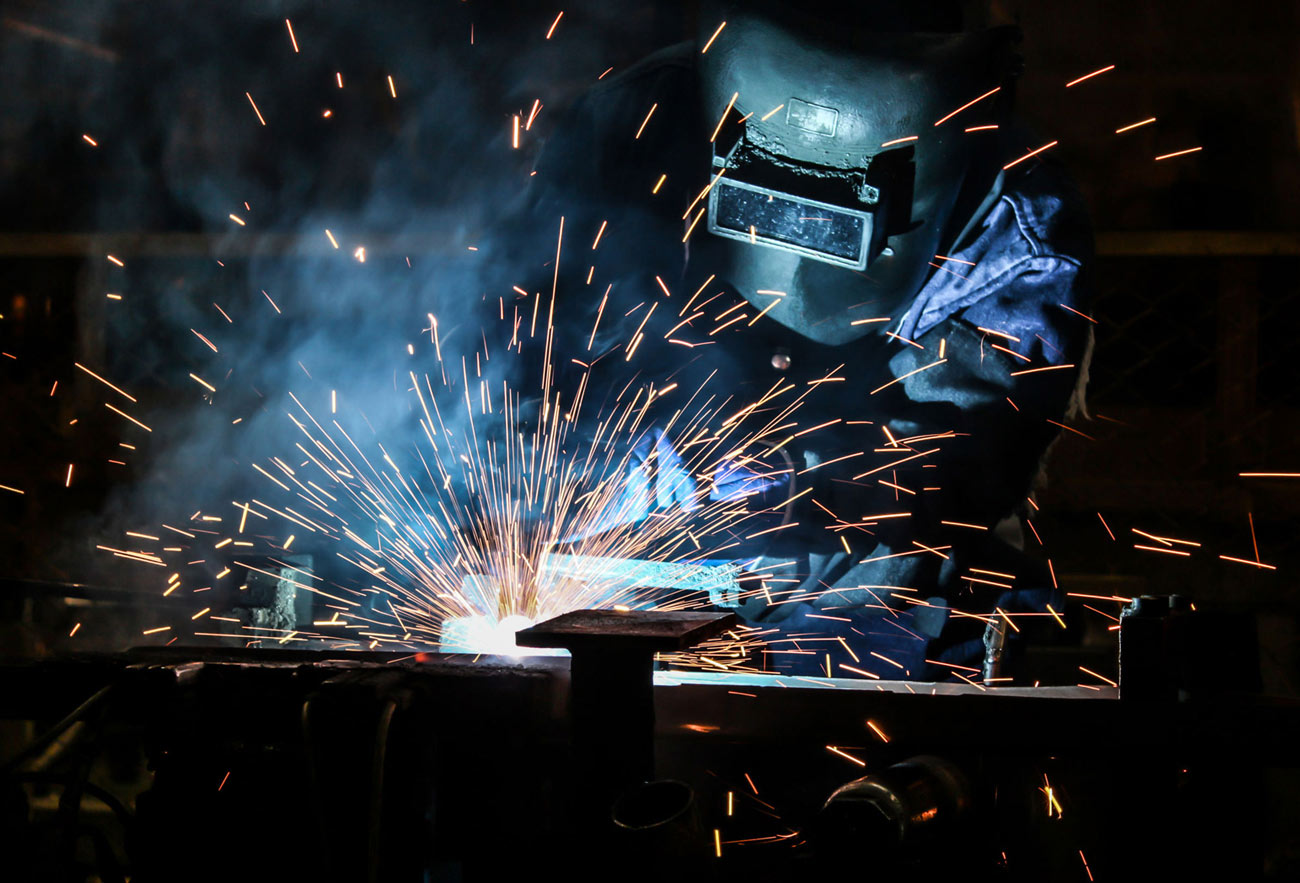
Weld Procedures
We can advise you on selection of pipe/plate diameters and thicknesses in order for you to obtain the maximum qualification range.
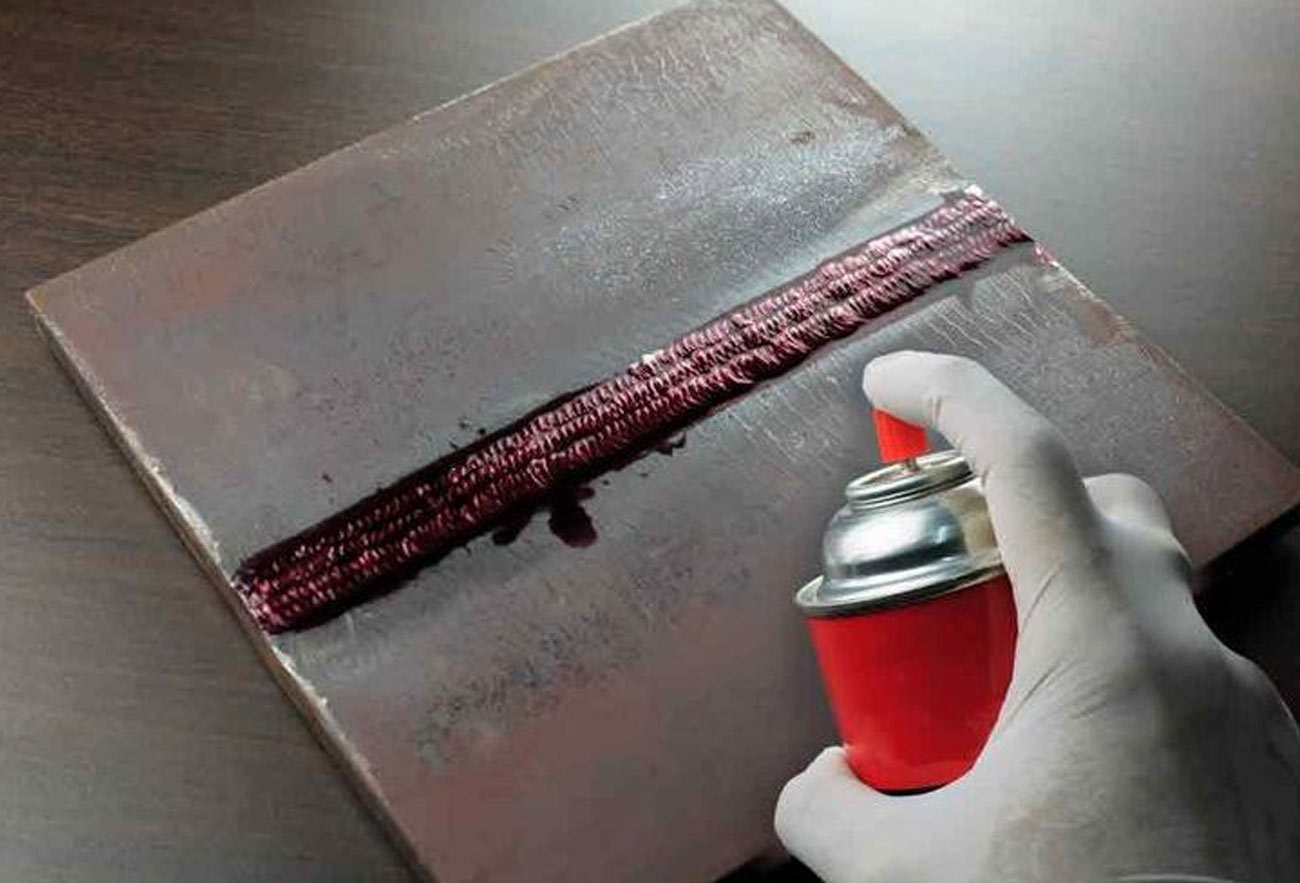
Liquid Penetrant Inspection
Although accepted as being the less sensitive method when compared to magnet particle testing for ferritic objects liquid penetrant inspection
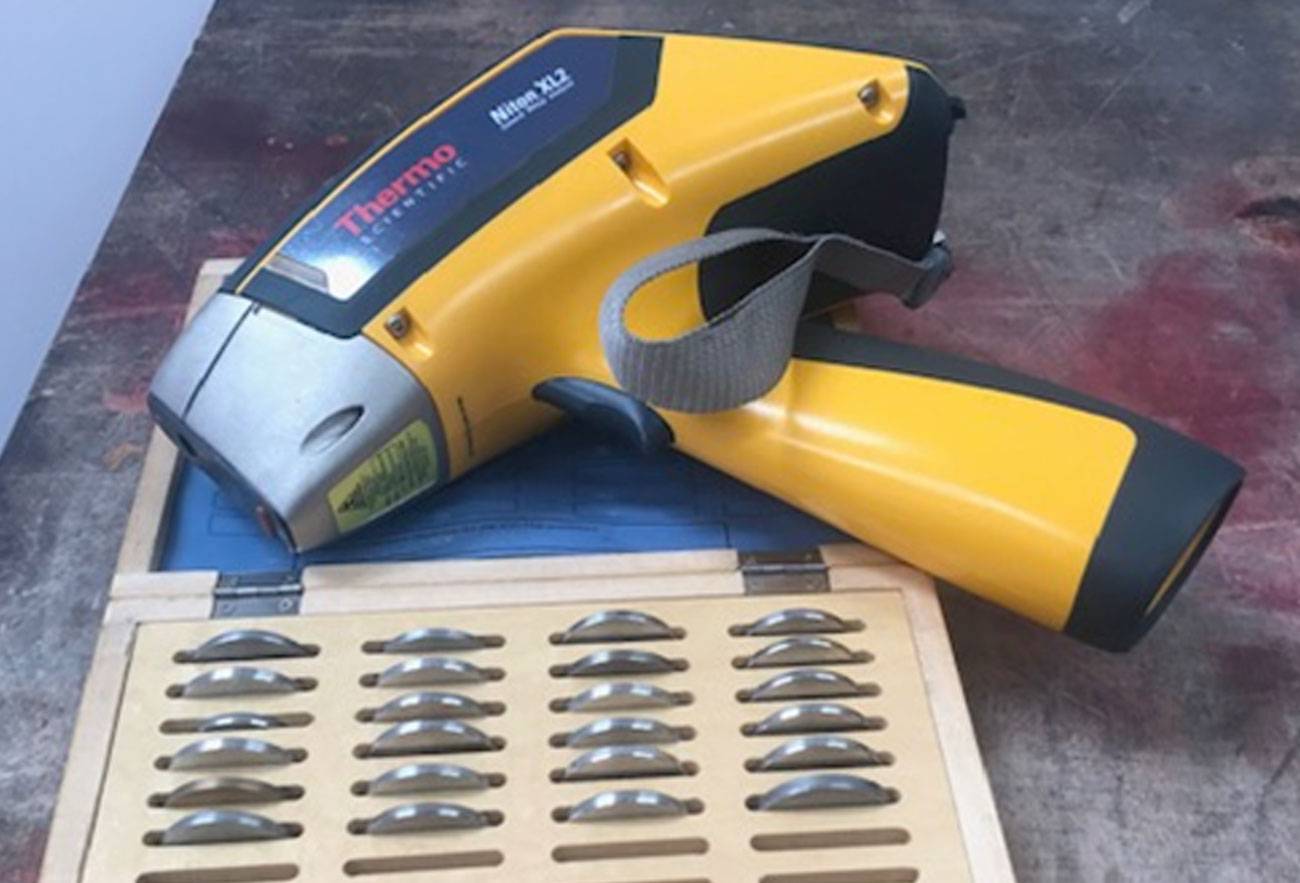
Alloy Verification - PMI
In the process of Alloy Verification the Niton XLt 898 is the ideal tool for performing Alloy Verification/PMI.
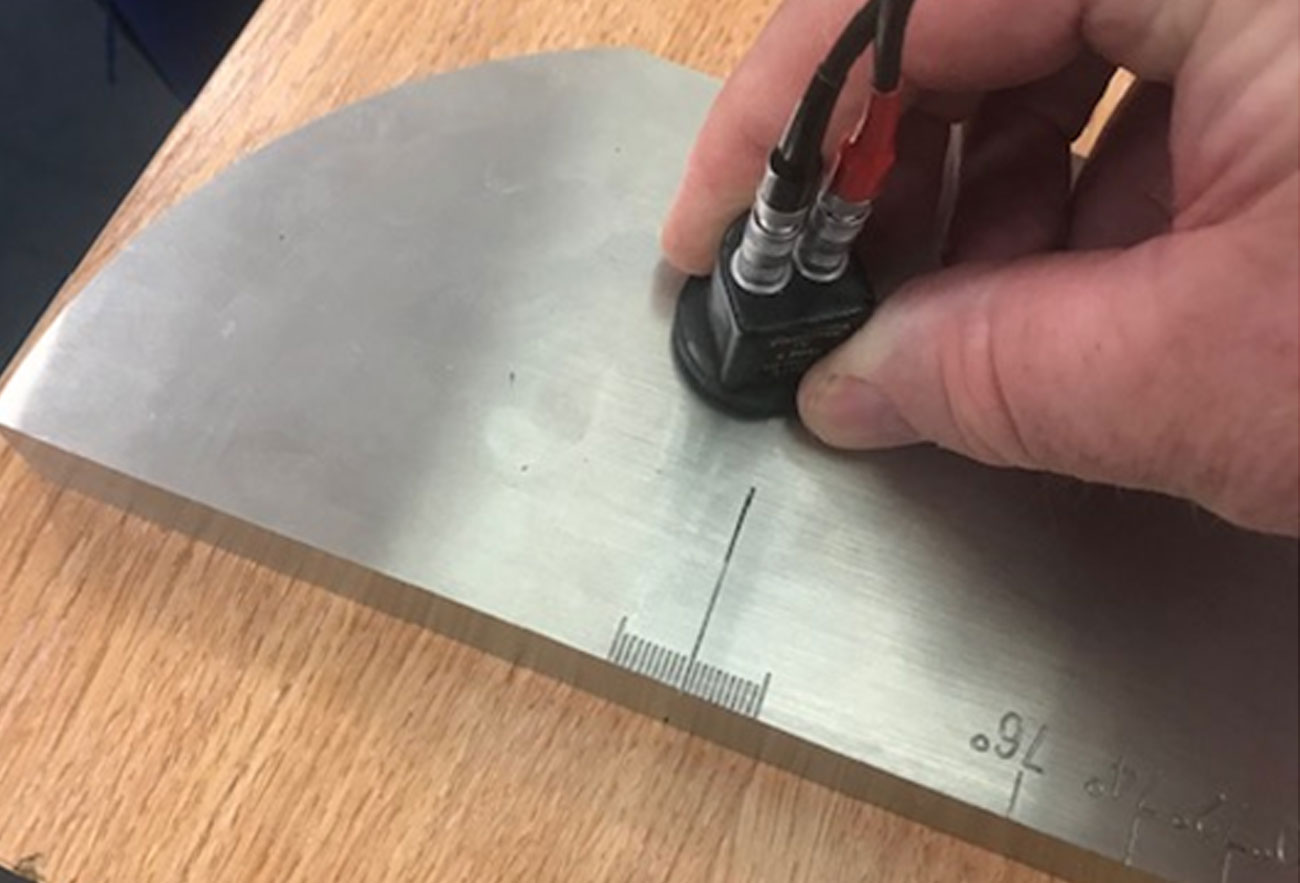
Ultrasonic Testing
Ultrasonic testing involves the sound travelling as a wave form through any given material with a constant velocity..
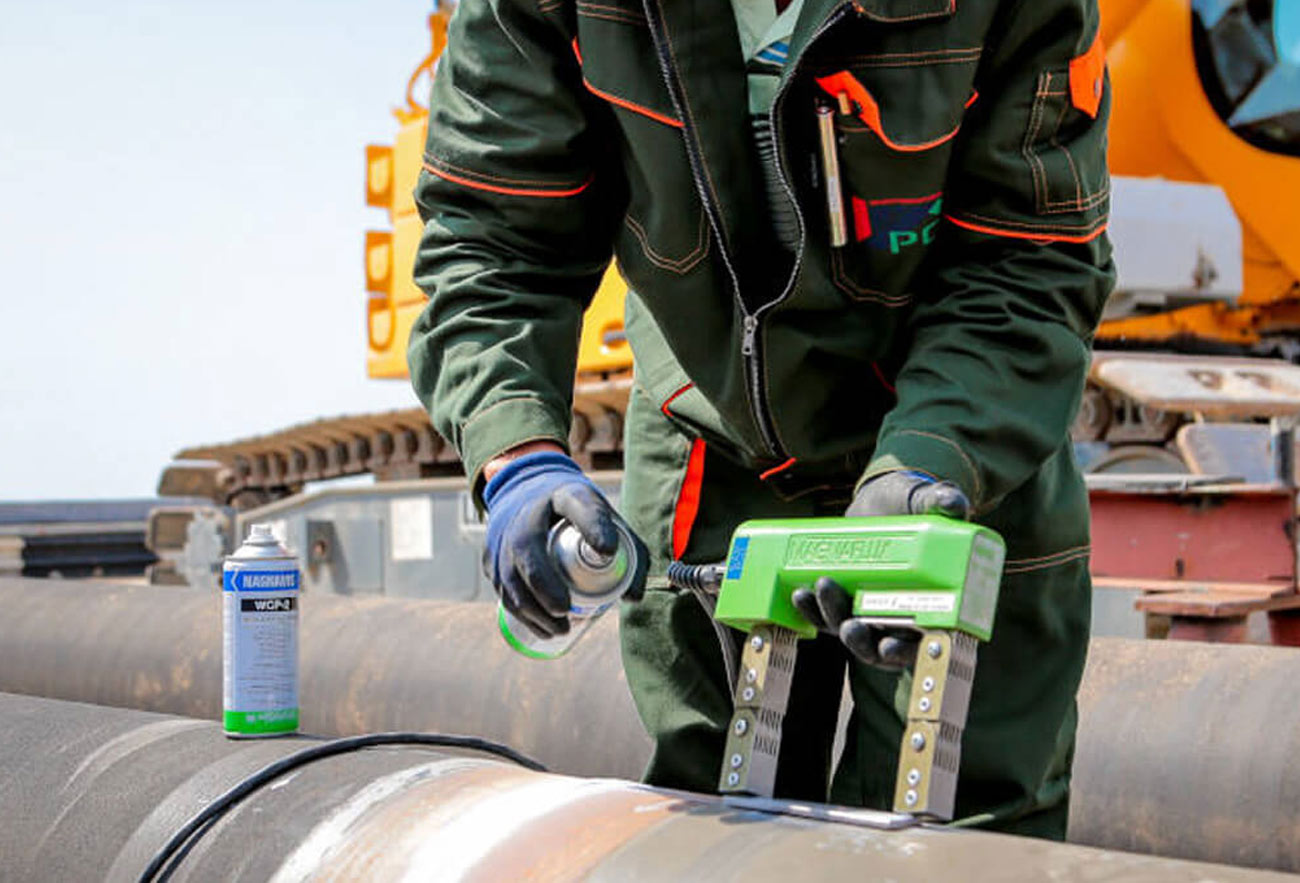
Magnetic Particle Inspection (MPI)
Magnetic Particle Inspection is used on Ferromagnetic materials in order to detect surface breaking flaws and occasionally sub-surface flaws.
FAQ
Most frequent questions and answers
It is common practice to use dye penetrant inspection (DPI) to find cracks in a surface. This non-destructive testing method, which is also called liquid penetrant inspection (LPI), is a cheap way to find surface-breaking flaws like cracks, pores, laps, seams, and other breaks in the surface.
DPT is based on the principle of CAPILLARY ACTION. Because of this, liquid tends to flow or seep into any small opening, even when outside forces like gravity try to stop it. This phenomenon occurs due to molecular attraction.
The chemicals used in dye penetrant tests typically include a penetrating liquid (dye), a developer, and a cleaner or solvent.
The dye penetrant process involves applying a penetrating liquid (dye) to the surface of the material being tested, allowing it to seep into any surface defects. After a specific dwell time, the excess dye is removed, and a developer is applied to draw out and make the defects visible.
The advantage of dye penetrant testing is its ability to detect surface defects, cracks, and discontinuities in various materials quickly. It is a cost-effective method that provides visible indications of flaws, allowing for timely repairs or further inspection if necessary.