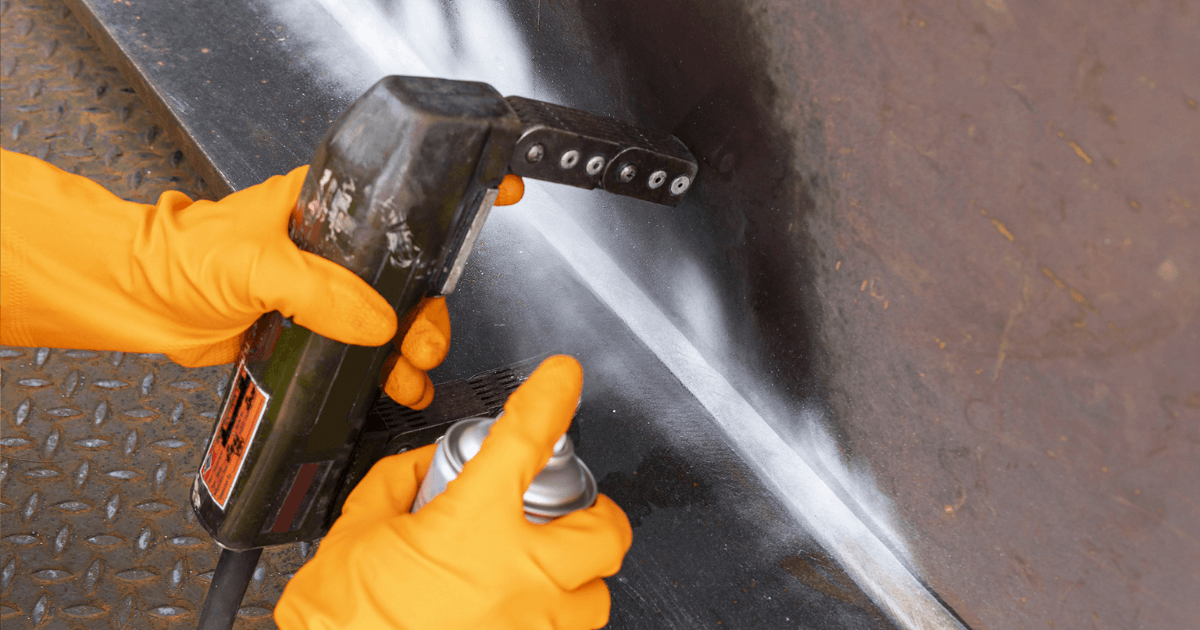
If you’re wondering why Magnetic Particle Testing is significant, this article is the right place to be!
A standard non-destructive testing method for detecting surface and subsurface discontinuities in ferromagnetic materials is magnetic particle testing (MPT).
The method uses magnetic fields and iron oxide particles to detect surface fractures, voids, and other faults that could affect the structural integrity of a material, and it is based on the principles of magnetism.
This blog will focus on the methods and uses of Magnetic Particle Testing and will examine its wide-ranging applicability in fields like aerospace, automotive, and manufacturing.
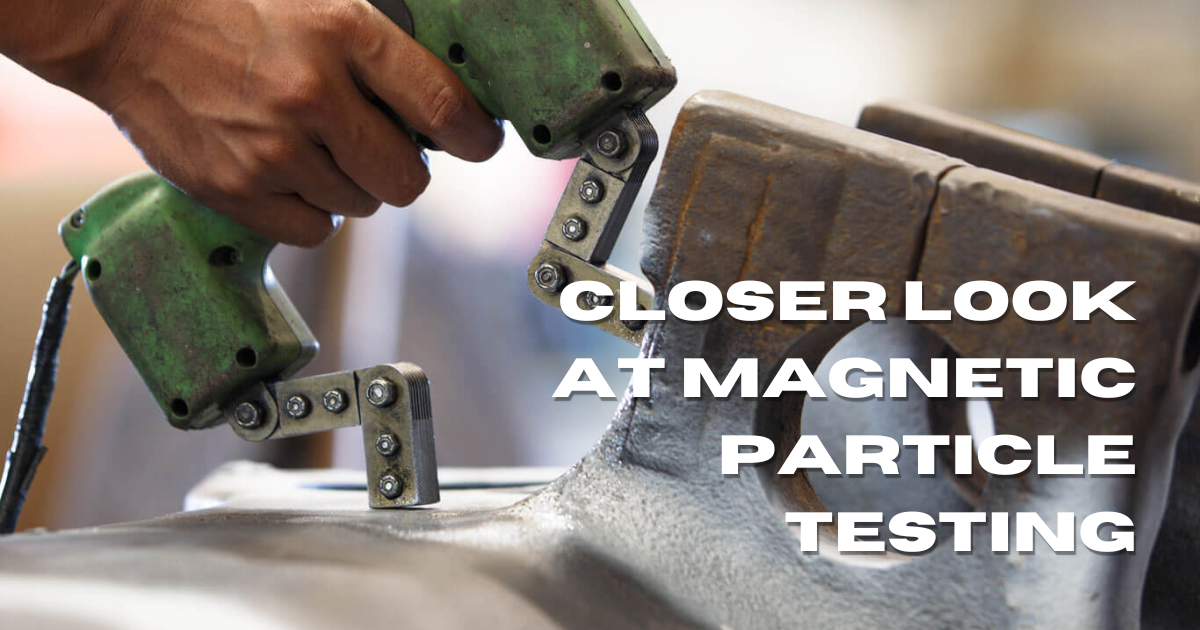
What Is Magnetic Particle Inspection: Principles & Techniques
Non-destructive inspection using magnetic particles can find linear defects close to the surface of ferromagnetic materials, hence the abbreviations “MT” and “MPI.” It is mainly considered a method for checking the outer layers.
When it comes to inspecting magnetic materials for flaws like cracks, porosity, cold laps, absence of sidewall fusion in welds, etc., Magnetic Particle Inspection (MPI) is a highly efficient technique.
There is a wide variety of methods available. The most adaptable method involves an electromagnetic yoke magnet powered by 110 volts of alternating current (AC), white stripped paint for contrast, and magnetic “ink” made of iron powder particles suspended in a liquid carrier base.
The yoke magnet is used to magnetise the area. If there is a defect on the surface or just beneath it, the lines of magnetic force will bend to avoid hitting the flaw.
By applying magnetic ink, iron powder particles can fill the void left by the flaw. As a result, the flaw becomes clearly visible against the white background.
Magnetic particle inspection (MPI) is widely utilised since it effectively finds flaws in Castings, Welded Fabrication, and Other Magnetic Products including the Identification of Cyclic Stress Fatigue Cracks.
Steps Of Magnetic Particle Testing
Magnetic Particle Inspection is performed in four steps:
- Induce a magnetic field in the specimen
- Apply magnetic particles to the specimen’s surface
- View the surface, looking for particle groupings that are caused by defects
- Demagnetise and clean the specimen
What Are the Advantages of Magnetic Particle Testing?
Magnetic Particle Inspection (MPI) is a non-destructive testing method that is often used because it has several advantages over other methods. Here are some of the key benefits of MPI:
Finds Surface and Subsurface Defects:
MPI is very good at finding surface and slightly subsurface defects in materials like steel and iron that are ferromagnetic. This includes cracks, voids, and other flaws that may not be visible to the naked eye.
Quick and Easy to Perform:
MPI is a relatively quick and easy inspection method that can be performed on-site. It doesn’t take much time to set up. Also, the equipment is portable, so it’s great for inspections in the field.
Cost-Effective:
Compared to other testing methods, MPI is relatively low-cost, making it an attractive option for many industries. It can reduce inspection costs while providing reliable and accurate results.
Versatile:
MPI can be used to inspect a wide range of components and structures, including pipes, tanks, and machinery. It is a versatile testing method that can be used in various industries such as aerospace, automotive, and manufacturing.
Safe and Environmentally Friendly:
MPI is a non-destructive testing technique that does not pose any health risks or harm to the environment.
Overall, the benefits of MPI make it a helpful testing method for many industries. It helps make sure that structures and parts are safe and reliable.
Applications Of Magnetic Particle Testing
Industries as diverse as aerospace, automotive, manufacturing, and oil & gas can all benefit from MPT. Pipes, tanks, and machinery parts are inspected for surface and subsurface defects including cracks, voids, and other flaws that could weaken the material’s structural integrity using this method.
In addition to finding flaws in ferrous materials like steel and iron, MPT can be utilised for weld inspection. It is an important way to test the quality and safety of buildings and parts across sectors. Because it can be changed and is always the same.
Closing Thoughts
MPI is important in the metal industry because it can find surface and subsurface flaws that could weaken the material’s structure.
Given the highly regulated markets of today, Gammax can be of great assistance in ensuring that your products as well as, your equipment meet national and international standards. Specifically, our team can inspect for magnetic particles on your behalf. However, to learn more about our services, please don’t hesitate to contact us today.