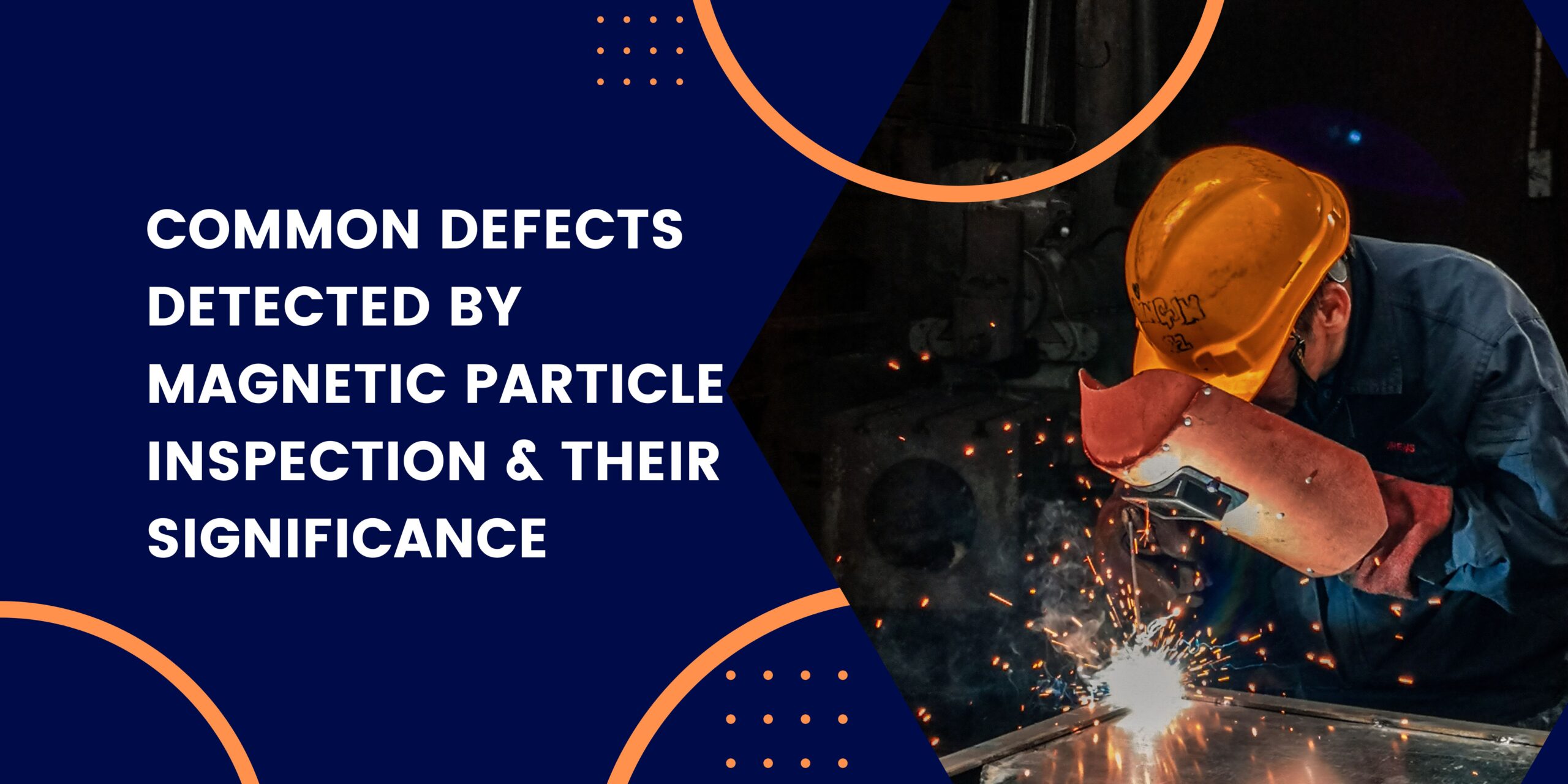
In this era of advanced manufacturing and infrastructure development, the significance of detecting and evaluating defects usingMagnetic Particle Inspectionandultrasonic testing servicescannot be overstated. As industries strive to maintain the highest quality standards, the precise detection and evaluation of defects using techniques like MPI and ultrasonic testing have become indispensable.
Magnetic Particle Inspection (MPI) is a widely used technique that utilises the principles of magnetism to identify surface and subsurface defects in ferromagnetic materials. Alongside MPI, Ultrasonic Testing Services provide an invaluable tool for detecting internal flaws and assessing the structural integrity of various materials. It uses high-frequency sound waves to identify defects such as voids, inclusions, delaminations, and thickness variations.
Gammax, among the pioneers in this field, is a trusted provider of advanced inspection solutions. Let’s talk in detail about the intricacies of magnetic particle inspection and ultrasonic testing services, exploring their capabilities, applications, and the benefits they bring to industries.
Surface Cracks
Surface cracks are fissures or fractures that occur on the external surface of a material. These cracks can significantly impact the structural integrity and reliability of a component or structure. Surface cracks are of great significance because they can propagate and lead to catastrophic failures if left undetected or untreated.
Magnetic Particle Inspection (MPI) is a highly effective method for detecting and evaluating surface cracks. MPI relies on the principle of magnetism to identify cracks by applying a magnetic field to the material under inspection.
The next step is to coat the material with a magnetic particle suspension, which draws attention to the magnetic field and gathers in places where surface cracks are causing magnetic flux leakage. Inspectors with training can easily identify and assess the visible indications created by this accumulation.
Subsurface Discontinuities
Subsurface discontinuities refer to flaws or defects that exist beneath the surface of a material, often hidden from visual inspection. These types of defects can include inclusions, voids, delaminations, or other irregularities within the material’s interior. It is essential to detect subsurface discontinuities, as they can compromise the mechanical strength, durability, and performance of a component.
Magnetic Particle Inspection can effectively identify and assess subsurface discontinuities through the use of suitable magnetisation techniques. By applying a magnetic field to the material, magnetic particles can penetrate the surface and accumulate at subsurface flaws. These flaws create magnetic flux leakage, resulting in visible indications that can be detected and evaluated during the inspection process.
Welding Defects
Welding defects are imperfections or anomalies that occur during the welding process. Common welding defects include porosity (gas pockets trapped in the weld), inclusions (foreign materials trapped in the weld), and incomplete penetration (insufficient fusion between weld and base material). These defects can weaken the joint, reduce structural integrity, and compromise the performance of welded components.
MPI plays a crucial role in detecting and evaluating welding defects. During the inspection, magnetic particles are applied to the weld surface, and a magnetic field is applied. If there are any surface or subsurface cracks associated with the welding defects, the magnetic particles will accumulate and create visible indications. This allows inspectors to identify and assess the size, shape, and severity of the welding defects accurately.
Fatigue Cracks
Fatigue cracks are progressive and often microscopic cracks that develop over time due to cyclic loading or stress fluctuations. They are of great significance because they can lead to sudden failure, even in structures or components that are initially defect-free. Fatigue cracks typically initiate at stress concentration points and can propagate under repetitive loading until catastrophic failure occurs.
MPI can find the magnetic flux leakage that fatigue cracks cause by applying a magnetic field and magnetic particles to the material. This allows for the detection of even small or hidden cracks that may not be easily visible during a visual inspection. MPI helps assess the size, shape, and extent of fatigue cracks, enabling timely actions to prevent catastrophic failures.
Trust Gammax For the Best Ultrasonic Testing Services
Obtaining high-quality Magnetic Particle Inspection (MPI) and Ultrasonic Testing Services ensures the integrity and reliability of critical components, preventing costly failures and ensuring operational safety. Accurate defect detection and evaluation provided by reputable service providers like Gammax enable industries to meet stringent quality standards, optimise maintenance strategies, and safeguard their reputation in a competitive market.
Our skilled NDT staff provides top-notch MT services to a wide range of industries throughout the United Kingdom. Please do not wait to get in touch with us to talk about the services you need. Contact us today!