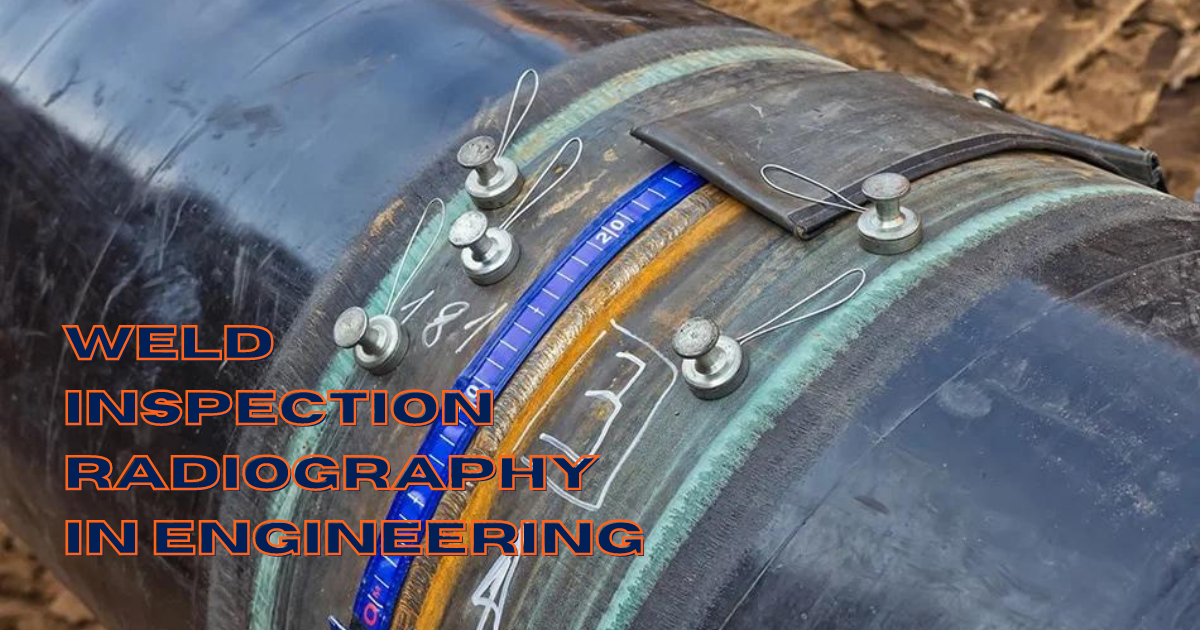
Welding is integral to various industries and is used for connecting two or more metal surfaces, machines and more. Once the necessary welding is done, inspecting the work to ensure there aren’t any flaws is pertinent. It will prove the quality of the work and eliminate the chance of malfunctions or accidents due to issues with the welding. Hence, weld inspection is a necessary aspect of every industry it is used in.
The importance and use of welds in different industries
Construction, aerospace, railways, vehicles and more industries employ welding daily and require proper inspection of the work being done. For example, aerospace is an industry where flawless weld work is necessary. It is also crucial to ensure the quality of the work done through proper inspection procedures. Radiographic testing or RT is a non-destructive testing method used for detecting defects with the weld without compromising the object or its components in any way. This method is used for inspecting materials and products, including welds, composites and casting. It can determine the quality of the welded joints from both sides.
Why is radiographic testing of RT used?
Radiographic testing confirms the best operational quality by showing details like changes in thickness, assembly details, and internal and external defects. The process may be slow, but it is highly effective for detecting issues like cracks, inclusions, porosity, voids and more in the internal parts of a weld. With the use of x-rays or gamma rays, RT produces a radiographic image of the target object. For x-rays, an x-ray tube is used, and for gamma rays, radioactive isotopes are employed.
Why is weld inspection necessary?
Though welding is an effective and strong method of connecting several metal surfaces and structures, it also gets damaged over time. Due to the varied environmental conditions and low-quality technology, small flaws will appear over time and turn into large defects. It may result in property damage, accidents and even deaths. Therefore, it is compulsory to check the quality, strength, safety and reliability of the welds being done. In every industry, welds and their quality are important. However, when it comes to aerospace, the importance increases exponentially because even the smallest flaw can result in the most tragic outcomes.
The methods of testing the weld quality and condition
Ensuring that the welds are done properly and that they do not have any flaws that can result in disasters is necessary. There are two different methods of testing the quality of the welds, the DT or destructive testing techniques and NDT or non-destructive testing techniques. Due to the nature of the techniques, NDT is the most popular method of checking weld quality and condition.
The principle of Radiographic testing of welds
You will be surprised to learn that the principles of radiographic inspection of welds and welding materials are very similar to those of medical radiography. They are:
- The radiographic film is kept on the remote side of the target object.
- Transmission of the radiation, whether x-ray or gamma rays emitted by an x-ray tube or radioactive isotope, respectively, happens from one side to the remote side where the film is already placed.
- The radiographic film determines the radiation and measures it in varied quantities over the entire surface.
- These radiographic films are then developed in darkroom conditions. The final image is viewed on a special light-emitting device.
- The images will be in different degrees of blacks and whites, and this will depend on the density of the radiation.
- This difference in the density of the processed film will be due to the discontinuities in the target material.
The advantages of using radiographic testing of the welds
Radiographic testing of welds has been designed to ensure various advantages for the users and their requirements for weld inspections. They are:
- Apart from the actual testing of the welds, RT can be used for detecting the volume of the target object.
- This testing facility comes with peerless quality control and helps detect flaws on the surface and subsurface.
- The results of such a test can be stored as a permanent record.
The importance of knowing the flaws
A weld may look flawless and strong from the surface, but only proper testing and inspection can determine the truth. When a welding project is in progress, it is vital to remember that it will not happen daily. You will not weld a section of any structure or surface every day. Therefore, you have to create something which can hold its own for a considerable period. Hence, it will be necessary to know about the possible flaws and find the methods to reduce or eliminate them. There can be different types of flaws, and you should be aware of them to be able to reduce them.
Having an idea about the methods used for finding and determining flaws in a weld will help you prepare for all eventualities and find the necessary solutions. For further details on the topic of hiring our service, please browse the relevant pages or get in touch with us.