Ultrasonic Testing
Ultrasonic testing involves the sound travelling as a wave form through any given material with a constant velocity characteristic of the material through which the waves are travelling.
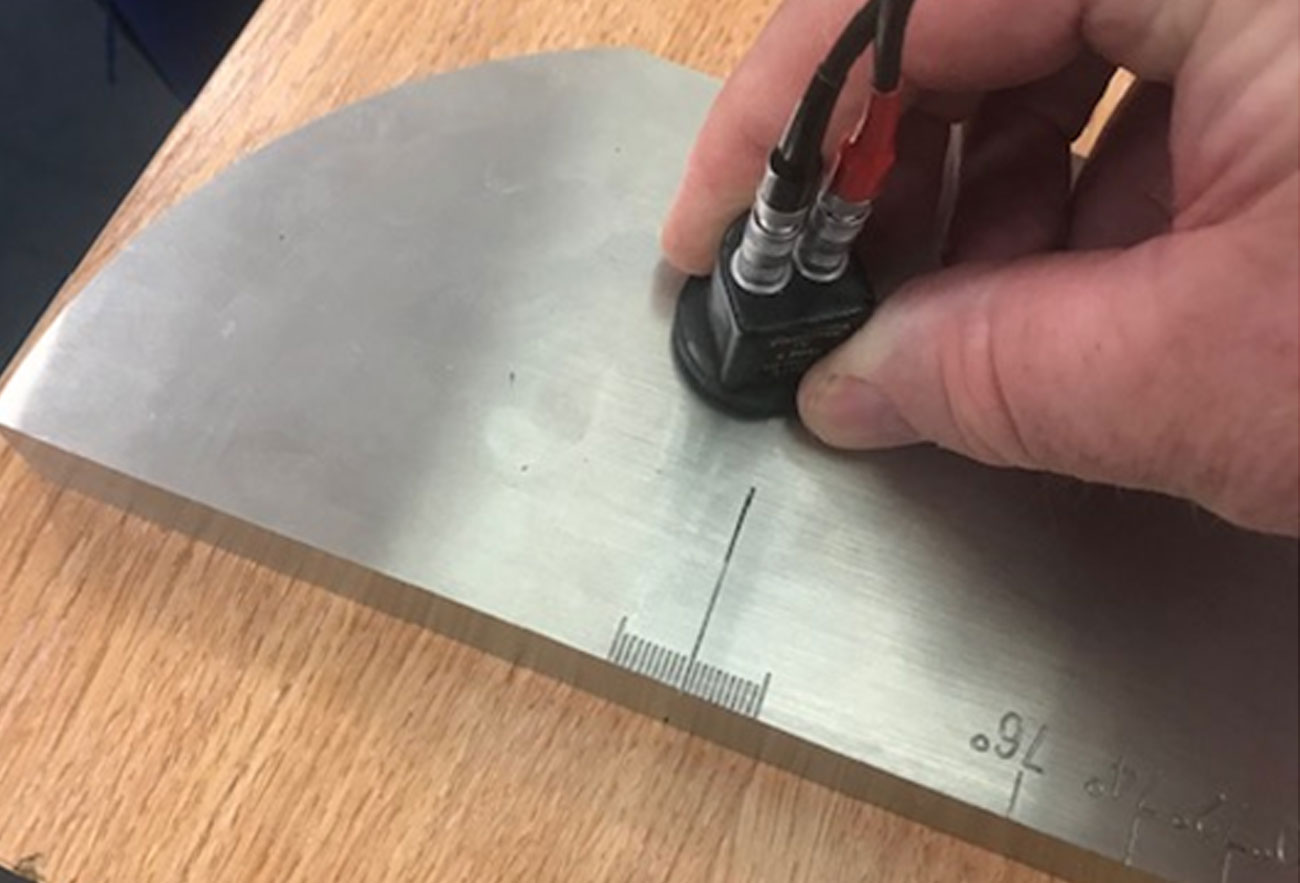
When ultrasonic sound meets an interface between two different materials, some is transmitted across the interface, but in general the greater proportion is reflected.
In pulse echo testing short bursts of sound – pulses – are transmitted into the test material at regular intervals using a transducer commonly referred to as a ‘probe’. Between pulses the ultrasonic flawdetector ‘listens’, awaiting the return of sound reflected back to the probe by any interface encountered.
The time elapsed from the point at which the pulse was transmitted to the point at which reflected sound remains is accurately measured. Thus the distance to the reflector can be accurately determined if the material velocity is known.
Ultrasonic testing is a powerful means of detecting both surface and subsurface defects in welds, castings and wrought products. It has an advantage over radiography in that it is particularly sensitive to planar defects such as cracks. Its effectiveness may be limited in some cases (because not all commonly encountered engineering materials are good conductors of sound).
Our Services
We test welds so that you don’t have to
- GIIS Ltd, Units 12-13, Oaklands Business Park, Bury St Edmunds, Suffolk, IP33 2RW
- 01284 850 888
- info@gammax.co.uk