Welding Procedures Specifications and Welder Qualifications
If your requirement is to obtain welding procedures and/or qualifications in accordance with BS EN ISO 15614, BS EN ISO 9606 or ASME IX then Gammax should be your first choice.
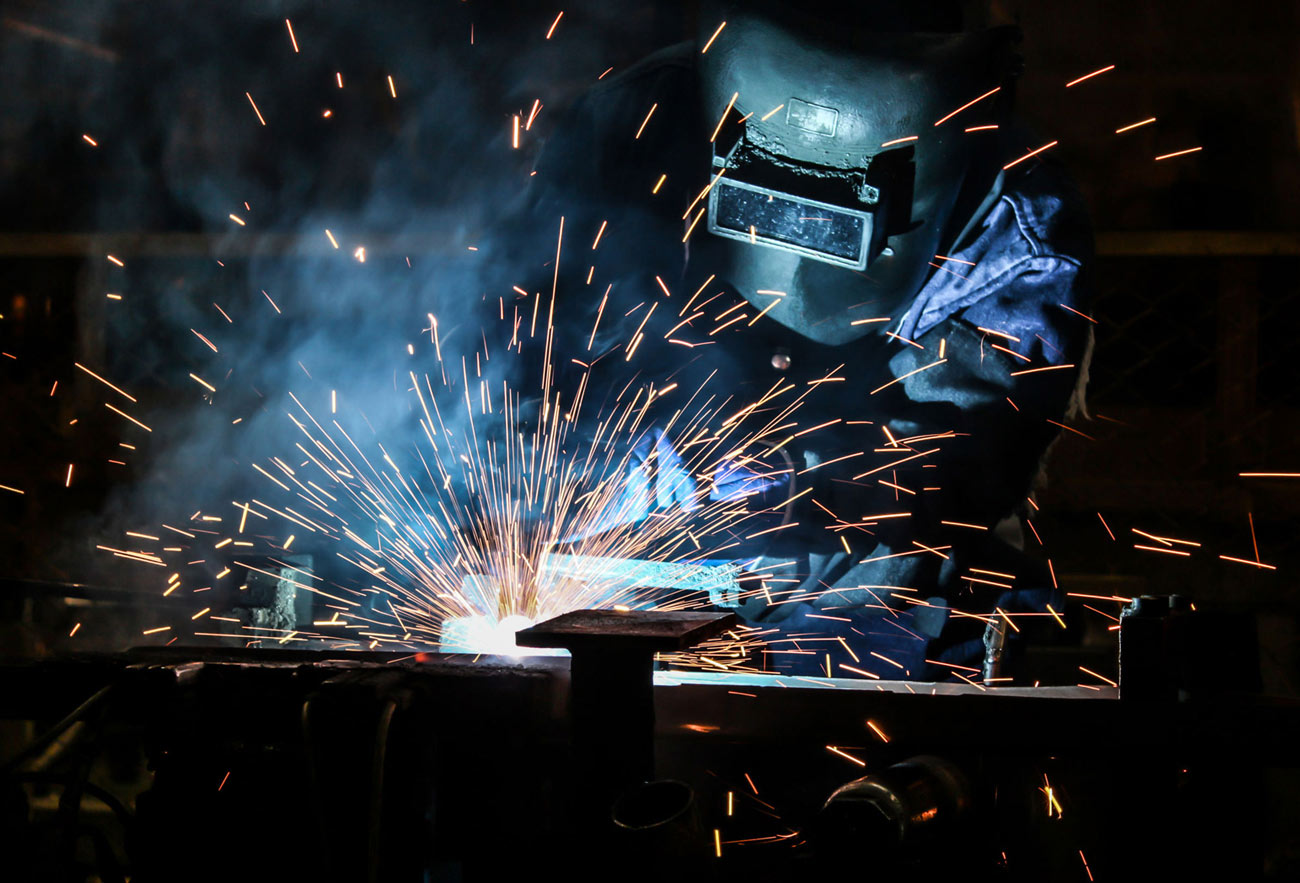
Welcome to Gammax Independent Inspection Services, your trusted partner in delivering top-notch welding procedures and related qualifications in the UK that are tailored to meet the highest industry standards. Here at Gammax we understand that precision, safety and quality are paramount in welding operations. Our comprehensive welding procedure services are designed to make sure that your projects meet stringent requirements while ensuring durability, reliability as well as compliance.
Why Choose Gammax for Your Welding Procedure and/or Welder Qualification Needs?
Expertise And Experience
With over 29 years of experience in the welding industry, we have developed a solid understanding of the complexities involved in welding procedures. Our team of certified welding engineers and inspectors brings unparalleled expertise to every project which ensures that each weld is executed with precision and care.
Comprehensive Services
Here at Gammax, we offer a wide range of welding procedure services to cater to various industries, including – construction, manufacturing, oil and gas and more. Our services include:
Welding Procedure Specification (WPS) Development: We create detailed WPS documents that outline the welding techniques, materials and parameters required for specific applications.
Procedure Qualification Records (PQR): Our team conducts thorough testing and documentation to qualify welding procedures. This ensures that they meet industry standards and client specifications.
Welder Qualification Testing: We provide comprehensive testing services to certify welders. This ensures they possess the skills and knowledge required to perform high quality welds.
Welding Procedure Review and Approval: Our experts can review and approve existing welding procedures in order to ensure that they comply with the latest standards and regulations.
Commitment To Quality
Quality is at the core of everything we do at Gammax. All our welding procedures are developed carefully and tested thoroughly to ensure safe and high quality welds. We adhere to national and international standards, including – ISO, ASME, AWS and EN to provide you with the confidence that your welding operations are in capable hands.
Cutting-Edge Technology
We use only the latest technology and equipment to enhance the accuracy and efficiency of our welding procedures. Our state-of-the-art facilities are equipped with advanced welding machines, testing equipment and software, which is how we can deliver superior results to our clients consistently.
Customised Solutions
Here at Gammax, we understand that every project is unique. Our team works closely with you to develop customised welding procedures that address your specific needs and challenges. No matter if you require procedures for complex assemblies or specialised materials, we can deliver tailored solutions that meet your specific requirements.
Types Of Welding Procedures We Provide
Here at Gammax, we specialise in the following four types of welding procedures and related qualifications to ensure each weld meets the highest standards of quality and compliance:
1. MAG Welding
Gas Metal Arc Welding, also known as MAG Welding, is a common type of welding where two metals that are to be connected are heated by passing a shielding gas along the wire electrode. This procedure, which covers plates and large bore pipes, requires a constant voltage and direct-current power source.
Modes Of MAG Welding:
- Globular transfer: The larger metal droplet size and the tendency for spattering during globular transfer result in a rougher weld bead. Thick metal plates can be horizontally welded using this technique.
- Short Circuit: Short-circuiting involves tapping the base metal repeatedly and quickly, several times per second, as the name suggests. This technique can be applied in any welding position because it generates less spattering.
- Spray Transfer: A steady-contact arc weld is maintained throughout the process during Spray Transfer. As a result of the steady contact tiny droplets of molten metal are produced. Despite the minimal spatter this technique creates, it works best with thick, flat horizontal pieces.
- Pulsed Spray: Spray Transfer and pulsed-spray are extremely similar, however, pulsed-spray uses a high-low current pulse to enable micro-cooling intervals. This method can be applied to a wide range of metal plate thicknesses and practically in all welding locations because of the way it is delivered.
2. TIG Welding
Tungsten Inert Gas welding, or TIG welding, is known for its precision and high-quality welds. This welding method is commonly used to join sections of stainless steel or non-ferrous metals. Here a fixed, non-consumable tungsten electrode is used in the arc-welding process to create the weld. It is considered as the most time consuming among all welding procedures.
3. MMA Stick Welding
Shielded Metal Arc Welding ( or MMA Stick Welding) is a reliable process used in the construction of steel structures as well as in industrial fabrication to weld iron, steel, and mild steel pipe using the open V-Groove. Here the welded junction is produced using a combination of electricity and consumable rod-shaped electrodes (welding rods) that have been coated in flux material.
To create an electrical arc between the electrode and the metal workpiece, an electric current is passed via the electrode. The electrode and the metal are both melted by this arc. The outcome is a mixture of molten metals made up of both the electrode and metal workpiece material.
4. Flux-Cored Arc Welding
Flux-Cored Arc Welding (FCAW) is ideal for welding thick materials and outdoor applications in building projects. This semi-automatic arc welding is an excellent substitute to MMA stick welding and offers portability and a fast welding rate. This process requires equipment similar to MAG welding, along with a continuous wire fed electrode and a power supply with a constant-voltage. However, it produces a huge amount of smoke which makes it unsuitable for indoor use.
Our Welding Procedure Services
1. Welding Procedure Specification (WPS) Development
A Welding Procedure Specification (WPS) is a critical document that outlines the welding process, materials and parameters required for a specific weld. Here at Gammax, we develop detailed WPS documents that serve as a roadmap for welders for ensuring consistency and quality in every weld. Our WPS development process includes:
Material Selection: We identify the appropriate materials for your project, considering factors such as – strength, corrosion resistance and weldability.
Process Selection: We choose the most suitable welding procedure, be it MIG, TIG, Stick, or FCAW, depending on your requirement and the application.
Parameter Specification: We specify the welding parameters, which include voltage, current, travel speed as well as heat input to achieve optimal results.
Joint Design: We also design the welding joints to ensure proper alignment, fit-up and accessibility for welding.
2. Procedure Qualification Records (PQR)
Procedure Qualification Records (PQR) or Welding Procedure Qualification Records serve as a validating document that ensures that your welding procedures meet industry standards. Our PQR services include:
Testing And Documentation: We conduct rigorous testing of your welds, including tensile, bend, and impact tests, to verify their mechanical properties.
Compliance Verification: We test your welding procedures to check if they comply with relevant standards and regulations. Based upon our findings, we provide you the necessary documentation for certification.
Performance Monitoring: We monitor the performance of your welding procedures over time and offer you advice regarding any adjustments that maybe needed to maintain quality and compliance.
All our welding procedure qualifications are written in accordance with BS EN ISO 15614 and ASME IX codes.
3. Welder Qualification Testing
We also offer welder qualification testing and certification, which helps you to demonstrate that your welders possess the qualifications required to maintain the quality and safety of your welding operations. Here at Gammax, we offer comprehensive welder qualification testing services, including:
Skill Assessment: We evaluate the skills and knowledge of your welders through practical tests and theoretical assessments.
Certification: We provide certification for welders who meet the required standards. This document ensures that they are qualified to perform specific welding tasks.
Ongoing Training: We also offer training programmes to help welders enhance their skills and stay updated with the latest industry techniques and standards.
Welding Procedure Review and Approval
We help you ensure that your welding procedures are up-to-date and compliant with the latest standards, which in turn assures their quality and safety. Our welding procedure review and approval process include:
Procedure Evaluation: We review your existing welding procedures and identify areas for improvement. This helps to ensure that they meet current standards.
Compliance Check: We verify if your welding procedures comply with relevant national and international standards, suggesting corrective measures wherever needed.
Approval And Documentation: After complete evaluation, we hand you formal approval and documentation for your welding procedures. This document serves as a proof that your welds are safe and reliable.
Contact Us
Ready to elevate your welding operations with Gammax? Contact us today to learn more about our welding procedure services and how we can help you achieve excellence in every weld.
Our Services
We test welds so that you don’t have to
- GIIS Ltd, Units 12-13, Oaklands Business Park, Bury St Edmunds, Suffolk, IP33 2RW
- 01284 850 888
- info@gammax.co.uk