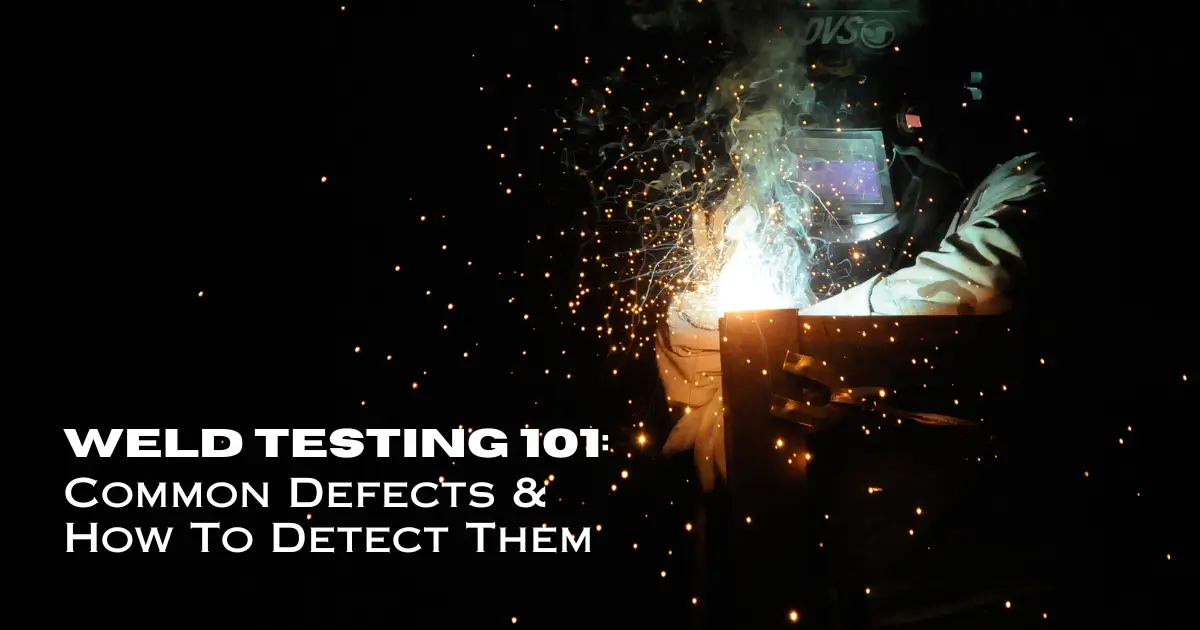
Welding is the backbone of countless industries, from construction to manufacturing. Ensuring welds’ quality and integrity is paramount, as even the smallest defect can compromise safety and structural soundness. That’s where weld testing comes in.
By performing careful weld inspections, we can find common flaws hiding in plain sight. These imperfections weaken joints and compromise entire projects, from porosity to a lack of fusion.
This blog covers everything in the world of weld testing, exploring its vital role and shedding light on the common defects that demand our attention.
Explore The Types Of Weld Defects & Their Causes
Porosity
Porosity occurs when there are tiny spaces or pockets of gas within a weld. It can result from several factors as below:
- Contaminants: Moisture, oil, rust, or dirt on the base metal or filler material can release gas during welding
- Improper shielding: Insufficient gas coverage or inadequate gas flow can lead to air contamination and porosity
- Inadequate cleaning: Insufficient removal of oxides or scale from the base metal can cause gas entrapment
- Incorrect welding parameters: Inappropriate heat input, travel speed, or electrode selection can contribute to porosity.
Lack of fusion
Lack of fusion occurs when there is incomplete bonding between the weld metal and the base metal or between successive weld passes. Here are a few reasons that can cause a lack of fusion:
- Insufficient heat input: Inadequate temperature or travel speed can lead to incomplete melting and fusion.
- Improper electrode angle: Incorrect electrode positioning may hinder proper fusion.
- Contamination: Dirt, rust, or scale on the base metal can impede fusion.
- Inadequate weld preparation: Insufficient beveling or improper fit-up can prevent proper fusion.
Cracking
Cracking in welds can manifest as hot cracks or cold cracks. Hot cracks occur during solidification, while cold cracks form after welding due to hydrogen embrittlement or stress. Here’s a list of the possible reasons for cracking:
- High cooling rates: Rapid cooling can lead to cracking, especially in materials prone to heat-affected zone cracking.
- Hydrogen presence: Excessive hydrogen introduced during welding can cause cracking.
- Residual stresses: Inadequate stress relief or improper welding sequence can result in cracking.
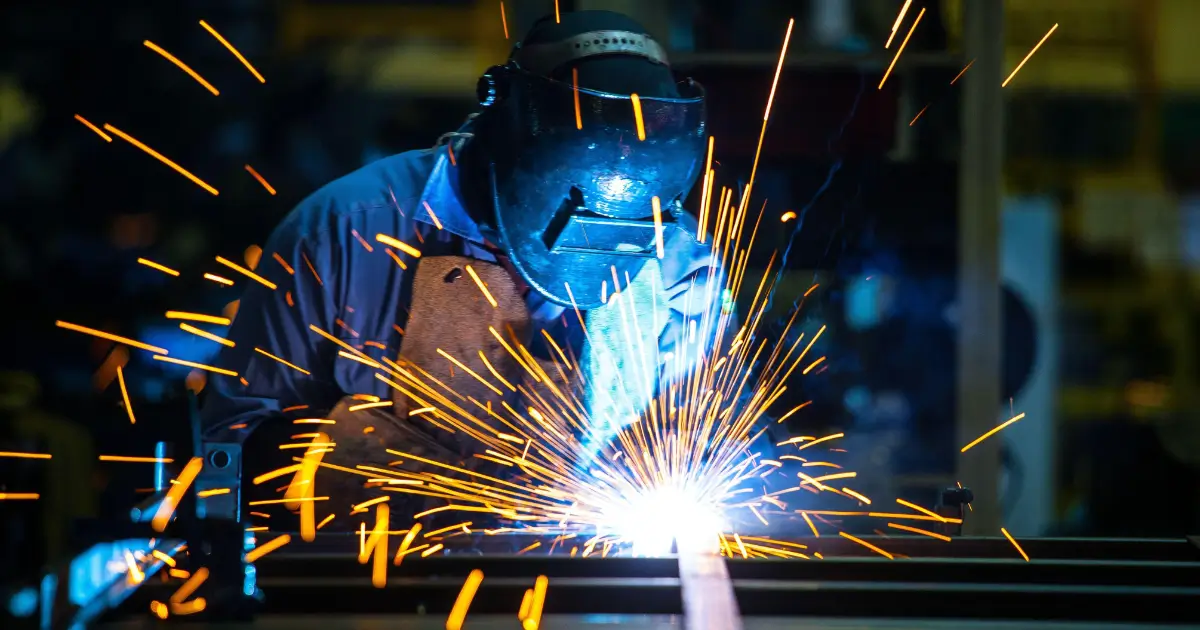
Weld Testing Techniques & Repairment For Each Defect
Porosity
Porosity can be detected through visual detection or NDT methods. Visual indicators of porosity include small round or elongated holes, often clustered in specific areas of the weld. Our trained inspectors visually examine the weld for visible signs of porosity. NDT techniques like ultrasonic testing or radiographic inspection can detect internal porosity.
Mitigation techniques for porosity include re-welding or repairing the affected areas by removing the porous sections and achieving proper fusion during welding.
Lack of fusion
Visual inspection and non-destructive testing (NDT) can also be used. Visual indicators of a lack of fusion include visible gaps or unfused regions between the weld and the base metal. Detection methods involve visual inspection by trained inspectors or non-destructive testing techniques like ultrasonic or radiographic inspection.
Remedial actions for lack of fusion may include re-welding the affected area to ensure proper fusion or employing techniques like preheating or adjusting welding parameters to enhance fusion.
Cracking
Weld inspection techniques for crack detection and analysis include visual inspection, dye penetrant testing, or radiographic inspection. Analysing crack characteristics helps determine the cause and potential preventive measures.
Repair methods for cracks depend on their severity and location. Techniques include grinding out the crack and re-welding or performing stress-relieving procedures. Preventive measures involve controlling cooling rates, reducing hydrogen content, and employing proper welding techniques to minimise stress and cracking risks.
Trust Gammax To Perform Only The Best Weld Testing!
Defects and flaws in welds can decrease efficiency and raise safety concerns at the workplace. Therefore, weld inspections help businesses save money by catching problems before they become an issue. The results of these inspections reveal details about the weld’s dimensions and quality, and most importantly, they highlight any flaws or deficiencies in weld joints.
Gammax Independent Inspection Services Ltd offers expert NDT weld testing services and keeps your operations compliant with UK welding standards. Using state-of-the-art equipment, our certified experts conduct comprehensive inspections of commercial and industrial structures, machines, plumbing, and more.
Get in touch if you want a no-obligation quote or to set up an appointment. Visit our website for more information.