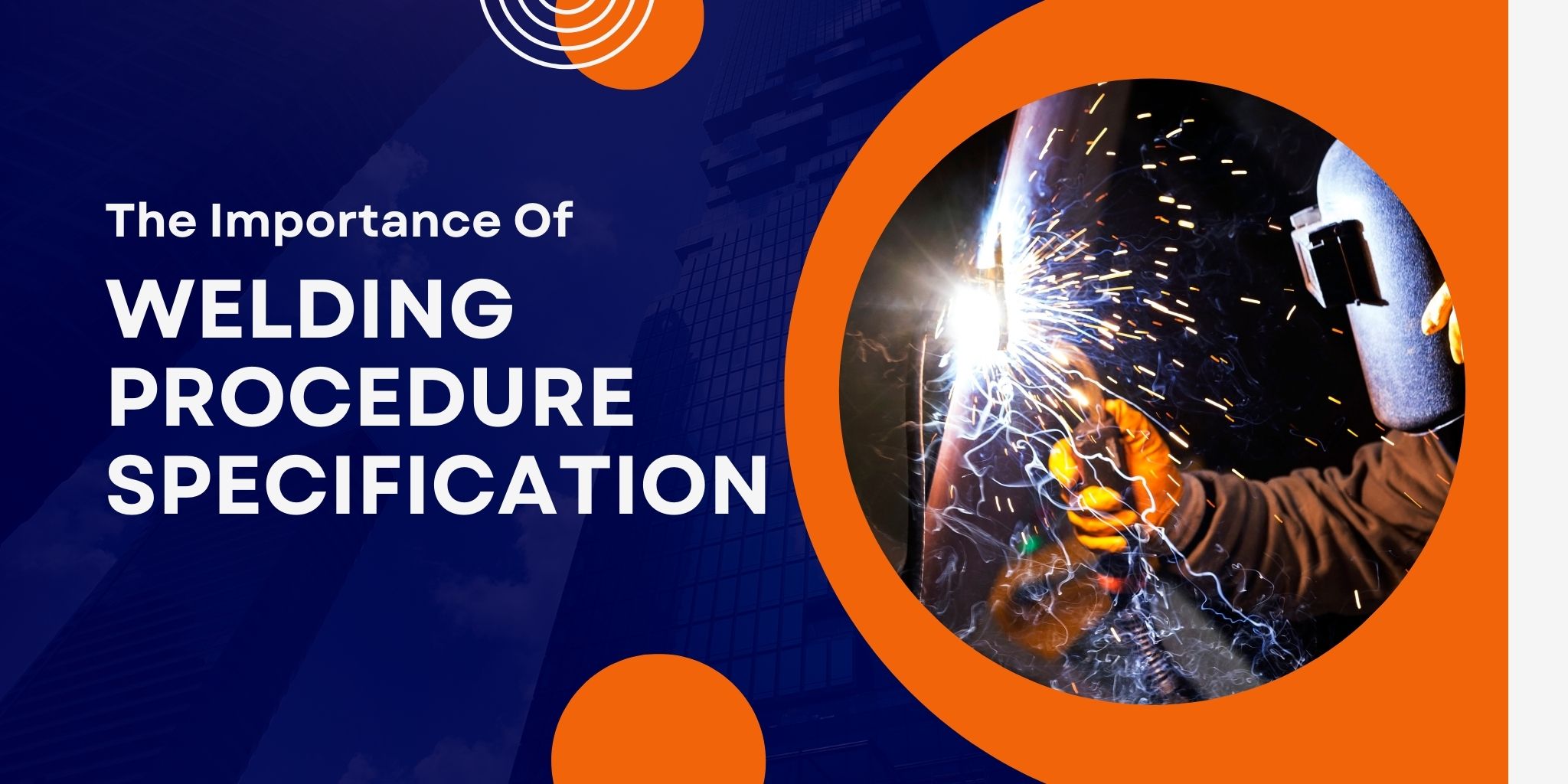
When it comes to welding, welders must meet specific standards for maintaining precision, safety and quality throughout their welds. A Welding Procedure Specification or WPS helps with this. It provides a detailed blueprint guiding welders as per the standard procedures required by industry codes. In this comprehensive guide, we will highlight the significance of WPS, the process of developing one and the advantages it offers in various welding operations.
What Is A WPS?
A WPS is a formal written document that describes standard welding procedures. It defines the entire welding process so welders can consistently create high-quality welds. A WPS specifies details such as the materials needed, tools required, processes to follow, and techniques to employ to maintain consistent welds throughout a project.
Why Do You Need Specification for Welding Procedures?
The necessity of a WPS extends beyond documentation. Here are some ways WPS can help in welding procedures:
Compliance With Regulatory Standards
Welding procedures within any project in the UK must adhere to the prevalent regulations to comply with industry standards. Failing to do so may lead to compromised quality or legal consequences. WPS bridges the gap between the theoretical standards and their practical application, thus ensuring that every task meets regulatory requirements.
Consistency In Welding Operations
Consistency is the hallmark of quality in welding. A WPS provides a set of standardised instructions, eliminating variability in welding practices. From intricate industrial welding to simpler fabrication projects, a WPS ensures each weld adheres to the same specifications, thereby enhancing overall consistency and reliability.
Quality Assurance Throughout the Welding Process
WPS does more than just ensure safety and compliance; it plays an important role in ensuring the quality of welds. By detailing the materials, techniques, and parameters used, WPS provides a framework for achieving precise and high-quality welds. This documented approach not only improves the quality of welds within projects but also provides a quality control mechanism for promoting better welding.
Streamlining Training and Knowledge Transfer
When it comes to welding, ongoing training and knowledge transfer are critical. Welding Procedure Specification provides a structured framework for learning for both new and seasoned welders. It ensures welders inherit practical skills and develop a deep understanding of industry standards and best practices, facilitating continuous professional development and skill enhancement.
Advantages Of Obtaining Specifications for Welding Procedures
Introducing a Welding Procedure Specification brings various advantages to welding projects, including:
Ensures Safety and Compliance
One of the primary advantages of a WPS is safety. It acts as a safety net by outlining the specific procedures and standards. This ensures each welder within the project adheres to industry regulations. WPS not only safeguards the well-being of those involved in the welding process but also helps to meet the stringent standards set by the regulatory bodies.
Enhances Consistency and Quality
Consistency is the key to welding, and WPS plays an essential role in achieving it. It eliminates variations in welding practices by providing a standardised set of instructions. These instructions allow welders to forge reliable and durable welds, improving project outcomes and facilitating easier inspection using non-destructive testing.
Improves Efficiency and Saves Time
A well-crafted WPS provides a detailed roadmap by streamlining the overall welding process for welders, which contributes to increased efficiency. It clearly defines the steps and parameters used in a welding procedure, thereby reducing the time spent on trial and error.
This gives a systematic and time-effective approach to welding. The increased efficiency benefits individual welding projects and contributes to the overall productivity of welding operations.
Boosts Confidence and Professionalism
With a specific design plan for each welding task, welders can proceed confidently. This confidence can then be conveyed to stakeholders and clients. WPS testifies to the seriousness with which welding projects are approached, which boosts the reputation of welders and welding companies.
How A Welding Procedure Specification (WPS) Is Written
Creating a complete WPS involves several steps, each of which is crucial for ensuring the document’s accuracy and reliability:
1. Identify Requirements
Collect everything needed for the weld, including the base materials and welding consumables. Go through the welding step by step and ensure anyone with the proper welder qualification can follow it.
2. Initial Welding Procedure Specification (IWPS)
After identifying all the required tools and procedures, draft a WPS. This document acts as a version that will undergo testing and improvements.
3. Welding Procedure Qualification Record (PQR)
This entails examining the weld to ensure it aligns with the WPS. This step confirms the precision of the PWPS, rectifying any mistakes or oversights before completing the WPS.
4. Ensure The WPS Is Completed
The completed WPS contains all details guaranteeing the accuracy and thoroughness of the welding procedures. This paperwork will undergo testing to confirm its dependability.
Types Of Welding Procedures Qualifications Gammax Can Help With
Here at Gammax Independent Inspection Services, we offer weld procedure qualification for the following welding procedures, each suited for different applications:
Manual Arc (MMA)
This old welding technique is still widely used, especially for outdoor and repair work. It requires high skill levels but is versatile and cost-effective.
Metal Inert/Active Gas (MIG/MAG)
This common and versatile welding process has high deposition rates and is suitable for various material thicknesses. It offers minimal weld finishing but requires maintenance of worn components.
Flux Cored Welding (FCW)
This is a form of MIG/MAG welding that uses self-shielding consumables, making it well suited for welding tasks. It offers deposition rates; however, it does leave behind a slag coating that requires removal.
Tungsten Inert Gas (TIG)
This is an arc welding process using a non-consumable tungsten electrode. It offers high-quality welds but requires a high skill level and is generally slower.
In Conclusion
A Welding Procedure Specification (WPS) is more than a piece of paper; it maintains safety, quality, consistency, and efficiency in welding tasks. Following an outlined WPS enables welders to produce top-notch welds that meet regulatory requirements and promote a culture of expertise and ongoing improvement.
Here at Gammax Independent Inspection Services, we are experts in various types of welding processes. We provide tailored welding solutions to clients across multiple industries in the UK. All our weld procedure qualifications are written in accordance with BS EN, ISO 15614 and ASME IX codes. Contact us today for assistance with Welding Procedure Specifications and qualifications.