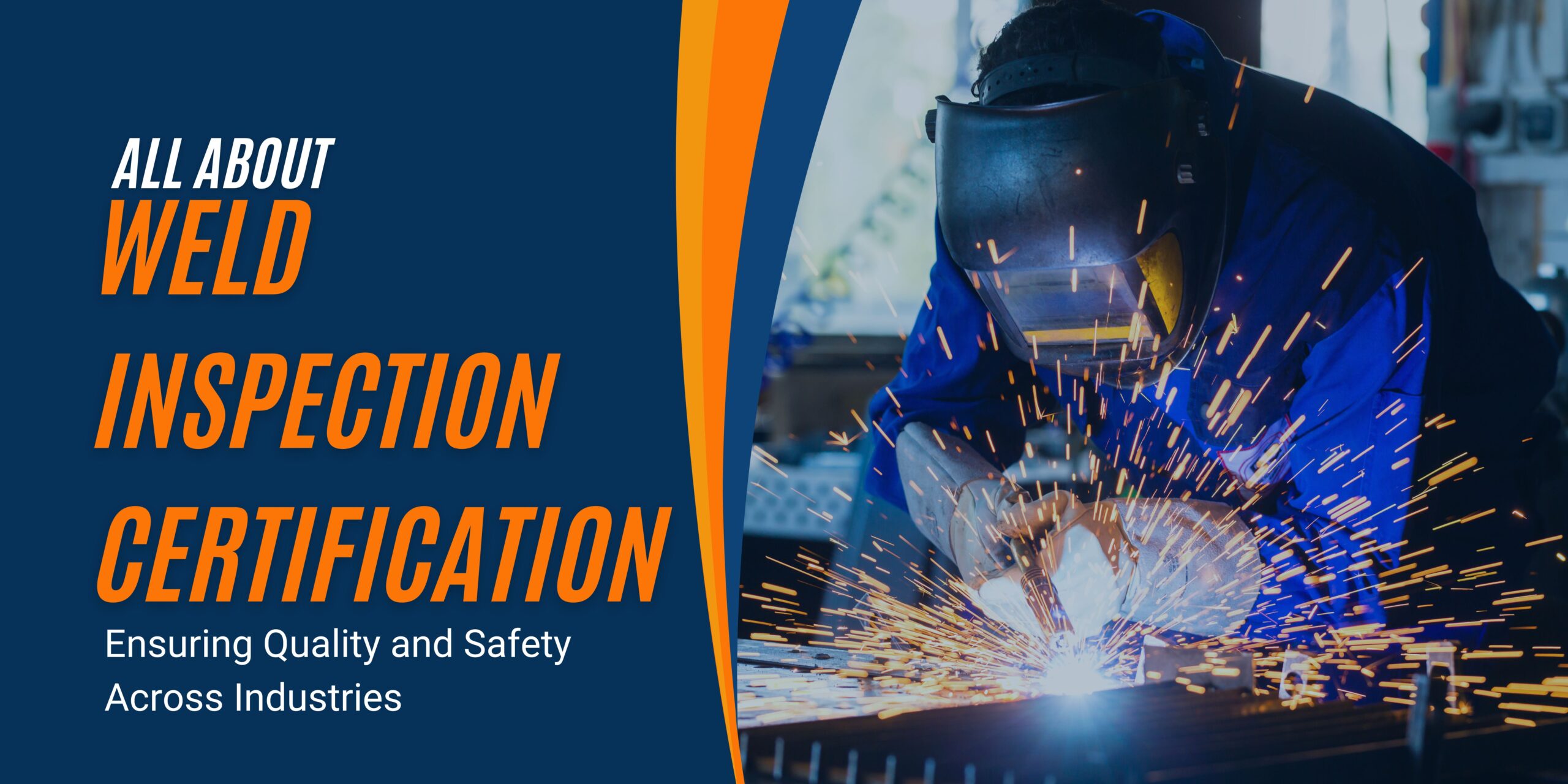
In various industries, welding is a vital procedure that gives components and structures strength and longevity. However, it is important to ensure the quality and integrity of welds to prevent failures that could lead to safety hazards and financial losses. This is where weld inspection plays a crucial role. In this comprehensive guide, we delve into the significance of gaining a weld inspection certification, its qualities, stages, common inspection techniques and the benefits it brings to industries. Before we delve into the intricacies, let’s take a close look at welds.
What Do Welds Do?
Welding is the process of joining metals together using extreme heat, which creates a bond that enhances the strength and structural integrity of materials. By melting the base metal and combining it with a filler material in a weld pool, welders create joints that are stronger than the individual components. Welds are essential in industries such as aerospace, automotive, construction, and manufacturing, where structural integrity is paramount.
Why Is a Weld Inspection Certification Important?
A weld inspection certification ensures that welded products meet specific criteria and acceptance standards, emphasising safety throughout the welding process. Weld inspection is crucial before, during, and after welding in order to identify any discontinuities or flaws that could compromise the integrity of the weld. By adhering to strict safety procedures and regulatory standards, weld inspectors help prevent safety issues and verify the quality of welded products.
What Are the Qualities of a Good Weld?
A good weld boasts a smooth, uniform appearance and adequate penetration into the parent material, which gives them a robust load-carrying capability. It signifies structural integrity and reliability, crucial for applications across diverse industries.
3 Stages of Gaining a Weld Inspection Certification:
1. Pre-Weld Inspection
Before initiating welding operations, thorough pre-weld inspections are essential. This stage involves ensuring compliance with safety measures, understanding job requirements, gathering materials and preparing the right tools and equipment.
2. During-Weld Inspection
During welding, continuous inspection is necessary to monitor heat input, cleaning between weld passes, welding technique and joint position. Visual clues are observed to identify potential problems and determine welding quality.
3. After-Weld Inspection
After welding, inspections are conducted to assess weld size, detect discontinuities or flaws, verify compliance with specifications and test weld strength using various methods.
Upon the completion of the entire inspection process, a weld inspection certification is issued, which indicates that all the welds within a project are up to the standard and do not pose any risks to the workers involved.
Common Weld Inspection Techniques Used:
Non-destructive Weld Inspections: These techniques aim to detect discontinuities without altering the welded piece. Some of the common methods for non-destructive testing include visual inspection, liquid penetrant surface crack inspection, magnetic particle weld inspection, radiographic weld inspection and ultrasonic weld inspection.
Destructive Weld Inspections: This involves the deliberate breaking of a welded piece to inspect its mechanical and physical traits internally. Techniques for destructive weld testing include macro etch weld inspection, transverse tension weld inspection and guided bend test weld inspection.
The Common Faults That Can Delay Your Weld Inspection Certification
Several faults can delay weld inspection certification, including inadequate weld penetration, lack of fusion, porosity, cracks and incorrect weld size or shape.
Benefits Of Getting A Weld Inspection Certification In The UK:
- Compliance with legal requirements and standards
- Assurance of quality and safety standards
- Prompt identification and repair of flaws
- Digitised inspection records for future reference
- Reduced risk of company liability
- Accurate detection of weld defects, ensuring structural integrity
Conclusion
Weld inspection certification plays a vital role in ensuring the quality, safety and integrity of welded products across various industries. By adhering to strict inspection protocols and utilising advanced inspection techniques, weld inspectors contribute to preventing safety hazards and maintaining high-quality standards.
Need Weld Inspection Certification? Contact Gammax Independent Inspection Services LTD
With over two decades of experience, we are one of the most trusted partners in the UK for anyone looking for non-destrcutive weld inspection certification. Our team serves diverse industries, from oil and gas to Formula One racing cars, ensuring safety and quality welds for all our clients. Our commitment to prompt response, adherence to international standards and team of highly qualified personnel provide affordable and top-notch inspection services in accordance with BS EN ISO 15614 and ASME IX codes. Reach out to us today for any non-destructive testing needs.