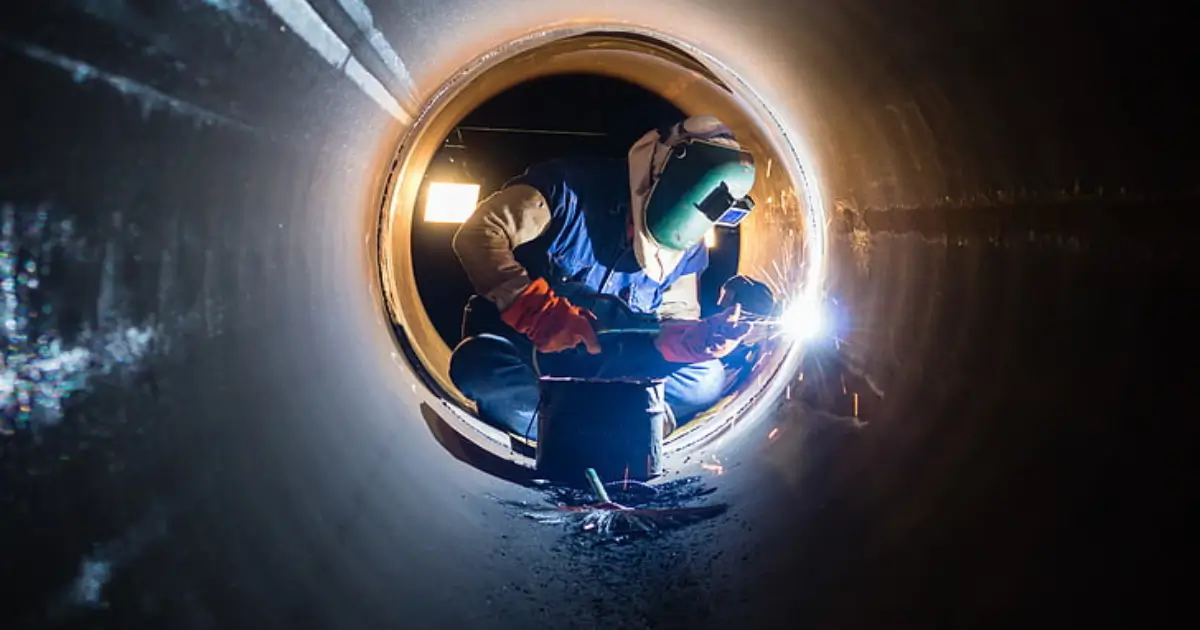
Welding is the process of joining two or more pieces of metal or thermoplastic together by melting the surfaces and then cooling and fusing them together. Welding procedures are classified into several types, each with its own set of characteristics and applications. Understanding the different types of welding procedures can help welders and businesses choose the best method for a project based on things like the type and thickness of the materials, the required strength of the weld, and how the finished product should look. Here, we will look at the most common types of welding processes and their distinguishing characteristics.
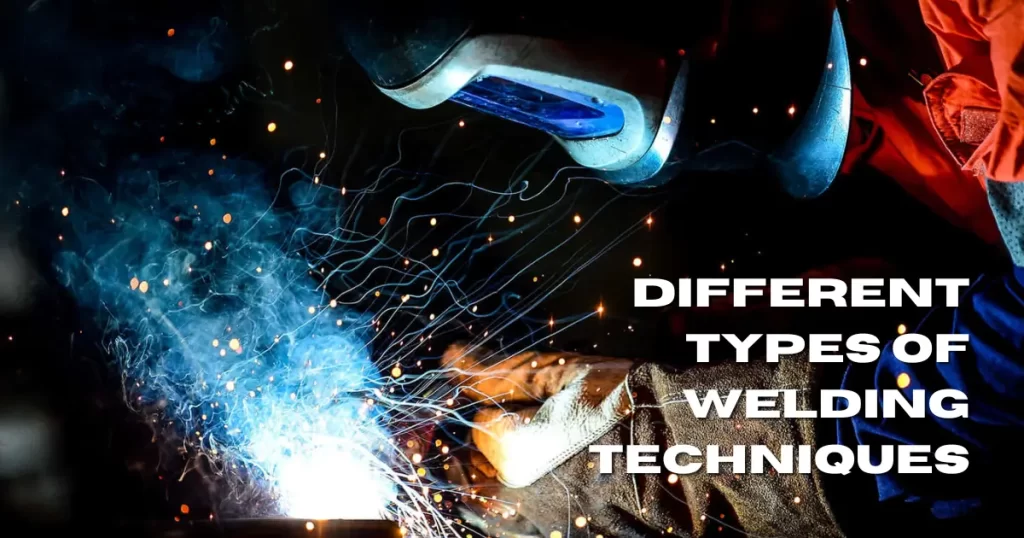
Four types of welding procedures are commonly used in industries:
Gas Metal Arc Welding Or MIG/MAG Welding (GMAW)
MIG/MAG welding is a simple and popular type of welding that even a novice can operate and master.
MIG welding, or gas metal arc welding (GMAW), is a semi-automatic process in which filler wire is fed through the gun and shielding gas is blown around it to protect it from environmental impurities. The filler wire is wound around a spool and used as an electrode as well.
The wire acts as an electrode, forming an arc with base metal that melts as filler material to form the weld. It is a continuous process, and the parameters must be set up ahead of time based on the welding needs. This versatile process is used for welding a wide range of metals and can produce smooth, clean and visually appealing welds.
The construction industry, automotive repair, robotics, plumbing, and the maritime industry mainly uses MIG/MAG welding. The welding produced by this process is strong and can withstand tremendous force.
Shielded Metal Arc Welding Or Stick Welding/MMA (SMAW)
These are century-old types of welding procedures that are constantly being improved. This kind of welding is popular because of its low cost and ease of operation. Essentially, the process can result in spatter welding that requires cleaning up.
A replaceable stick electrode serves as the filler material in this case. The arc is created when the end of the stick makes contact with the base metals. The arc’s heat melts the electrode’s filler metal, resulting in the weld. It coats the stick electrode with a flux that forms a shielding cloud, preventing oxidation of the weld zone. On cooling, the flux transforms into slag, which must be chipped away.
The process has the advantage of being able to be performed outdoors in adverse weather conditions such as wind and rain. It is useful in equipment repair because it can be performed on rusted, painted, and dirty metals. Stick welding/MMA is a skill that takes a long time to master.
Gas Tungsten Arc Welding Or TIG Welding (GTAW)
TIG welding can be performed without filler material. When the non-consumable tungsten electrode comes into contact with the base metal, it creates an arc. The powerful arc melts and joins the two metals. You require a constant shielding gas supply to protect welding from environmental impurities. These types of welding are more effective indoors and away from the elements. TIG welding produces strong welds but is difficult to master. Only an experienced welder can perform this art of welding because it requires the use of both hands at the same time. TIG welding produces precise, strong and visually appealing welds, requiring no cleanup. It can easily weld stainless steel, aluminium, magnesium, nickel, and copper. The process is widely used in nonferrous metal industries such as tubing, bicycles, and vehicle manufacturing. It is appropriate for repairing tools made of aluminium, magnesium, and stainless steel.
Flux-cored arc welding (FCAW)
Because the same power source can perform both types of welding, FCAW is a lot like MIG/MAG welding. Filler wire is used as an electrode in MIG/MAG welding and is fed continuously from the gun. In contrast, FCAW uses a wire with flux and creates a gas shielding zone around the weld. In this type of welding, no external shielding gas is required. This method is adaptable and suitable for thick metals.
With high-heat welding, the welding process is efficient and effective for heavy metals. Because there is no need for external gas, it is less expensive than other types of welding. It is useful for thicker metal and is used to repair heavy machinery. However, you must clean up the flux slag to get a beautiful, clean weld. This type of welding can easily be done outdoors because no shielding gas is required.
How can Gammax Independent Inspection Services help you with different types of welding?
At Gammax, we provide you with certified welder qualifications for all four types of welding procedures, as well as related qualification services. We can advise you on pipe and plate diameters and thicknesses in order to achieve the maximum qualification range possible. We also inspect your welds to ensure safety and efficiency.
The Welding Institute’s Welding Qualifier software is used to write our welding procedures and qualifications in accordance with UKAS’s accreditation to ISO 17020.
Conclusion
Hiring certified welders is the only way to make sure that welding jobs are done safely, correctly, and quickly. Certified welders have undergone extensive training and proven their ability to perform welding tasks in accordance with industry standards. By hiring certified professionals, companies can avoid making expensive mistakes, lower the risk of accidents, and ensure that their welding projects are done to a high-quality standard. Investing in certified welders will help any welding project be successful and safe in the long run.
To learn more about the types of welding, we provide, please visit our website.