Magnetic Particle Inspection | Non Destructive Weld Test Procedure
Magnetic Particle Inspection is used on Ferromagnetic materials in order to detect surface breaking flaws and occasionally sub-surface flaws.
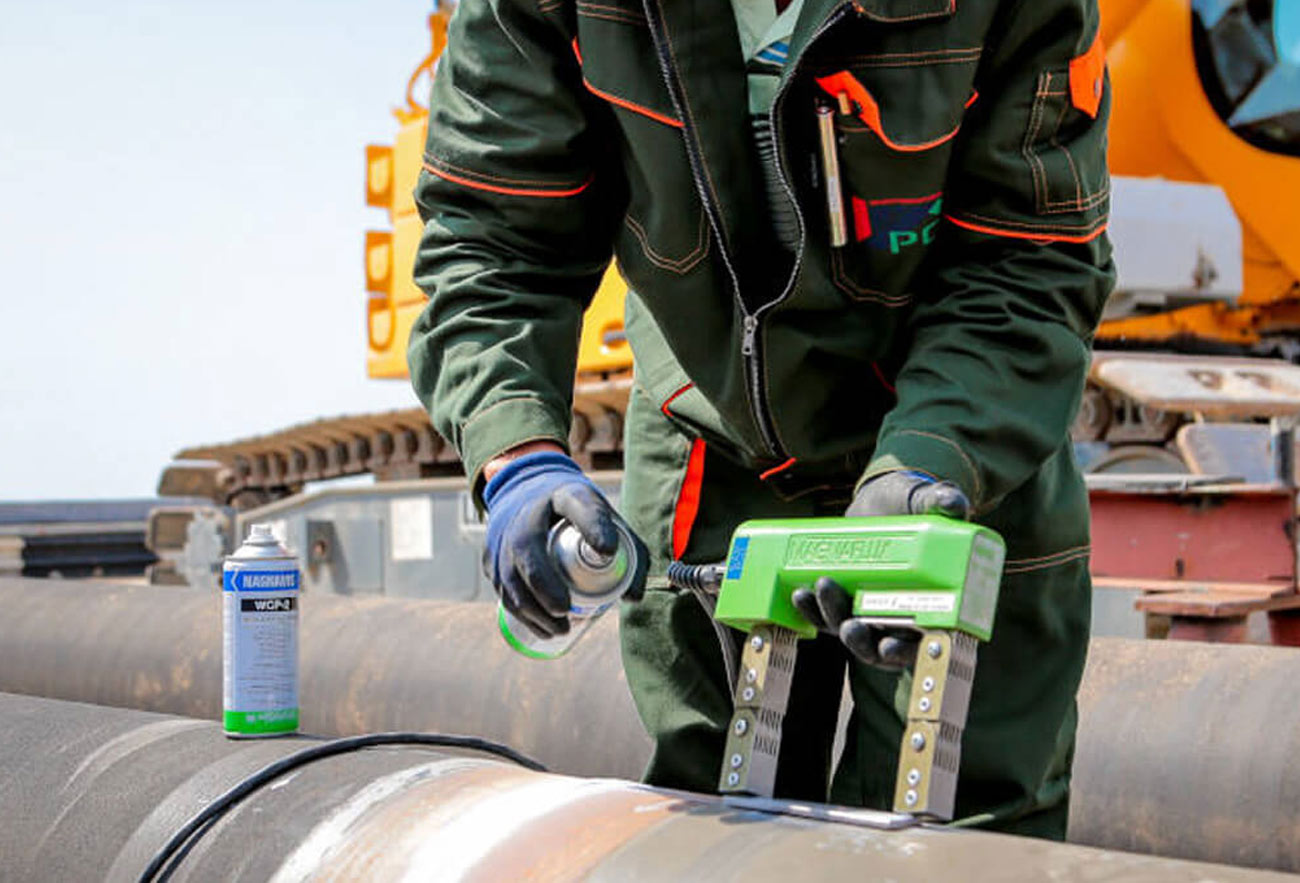
At Gammax Independent Inspection Services Ltd., we offer Magnetic Particle Inspection (MPI) as a non-destructive testing method for detecting surface and near-surface flaws in ferromagnetic materials. This advanced technique uses an induced magnetic field to test the integrity of components and is applied in various industries, including aerospace, automotive, power generation, and construction.
Let’s take a look at the crucial role MPI plays across industries…
The Importance of Magnetic Particle Inspection
Magnetic Particle Inspection is critical for ensuring components’ safety, reliability, and longevity across various industries. This inspection method helps detect and identify defects early on, thus helping prevent damages, reduce downtime, and improve product quality.
Here’s Why MPI Is an Ideal Choice for Various Industries:
Safety: MPI helps in the early detection of defects, which prevents accidents and injuries. For example, when this inspection method is used to inspect critical components in aircraft, such as engine parts, landing gear, fuselage and other critical components, it evaluates if they are free from defects that could otherwise lead to catastrophic incidents.
Reliability: By identifying defects, magnetic particle inspection allows you to perform early repairs to improve the reliability of components. This can be especially beneficial for critical power generation and transportation components, where failures can have serious consequences.
Product Quality: MPI helps ensure that products are defect-free and meet the strict quality standards in various industries. This ensures that you supply good-quality products to customers that keep them satisfied and improve brand reputation.
Cost-Effectiveness: MPI is a non-destructive testing method for inspecting components. Identifying and repairing defects early on reduces the money you would have otherwise spent on repairs and replacements.
What are the Types of Magnetic Particle Inspection?
There are two primary types of MPI:
- Dry Magnetic Particle Inspection: Here, dry ferromagnetic particles are applied to the magnetised surface to detect faults. This method is suitable for inspecting rough surfaces and surfaces with large areas.
- Wet Magnetic Particle Inspection: In wet MPI, ferromagnetic particles are suspended in a liquid carrier, such as water or oil, to detect faults. This highly sensitive technique effectively detects fine surface cracks and subsurface defects.
How Our Magnetic Particle Inspection is Carried Out:
- Cleaning: Our process begins with thoroughly cleaning the surface to remove any contaminants, such as dirt, grease, or rust, that may interfere with the inspection. Proper cleaning ensures that the magnetic particles can adhere to it and accurately reveal any defects that may be present.
- Paint Application: After cleaning the surface, we apply a thin layer of contrast paint to enhance the visibility of any defects the magnetic particles indicate. The paint we use will vary depending on the type of magnetic particles used and the lighting conditions for the inspection.
- Magnetisation: Once the paint has dried, we will induce a magnetic field into the material using various direct and indirect magnetisation techniques, such as:
- Using a permanent magnet or electromagnet on the surface to create a magnetic flow
- Passing current through the material, creating a current-induced magnetic field
- Placing the specimen inside a coil or forming a coil around it and passing current through the coil
- In the case of ring-shaped specimens, using it as the secondary loop of a transformer
- Placing the specimen near a current-carrying coil or loop
- Placing a current-carrying rod through hollow specimens
Using the appropriate magnetisation technique, we ensure the strength and direction of the magnetic field induced are sufficient to saturate the material. This means that all of the magnetic domains in the material are aligned in the same direction. This alignment is necessary to ensure that any defects in the material disrupt the magnetic field and cause magnetic flux leakage, attracting the magnetic particles.
- Particle Application: After properly magnetising the material, we apply fine ferromagnetic particles (either dry or suspended in a liquid) to its surface. The type of particles we will use for a specific Magnetic Particle Inspection will depend on the defect being inspected and the sensitivity required. For example, dry particles are typically used for inspecting larger areas, while wet particles are usually used for inspecting smaller areas or detecting fine surface cracks.
- Evaluation: Following the application of magnetic particles, our experienced inspectors will carefully examine the surface and look for visible defects. Wherever any magnetic flux leakage occurs caused by defects, the magnetic particles will get attracted to those areas, forming patterns. We will use a variety of techniques, including visual inspection, magnification, and measurement, to evaluate these indications, which will help us determine the flaw’s location, size and orientation
- Demagnetisation: Once the inspection is complete, we demagnetise the material to prevent any adverse effects on subsequent operations or future inspections. We typically demagnetise by passing the component through a demagnetising coil or applying a decreasing alternating current.
Application of Magnetic Particle Inspection
Magnetic Particle Inspection is used in various industries for fault detection, including:
- Aerospace: To inspect different components of an aircraft, such as engine parts, landing gear, fuselage and other critical components.
- Automotive: To inspect the integrity of automotive components like engine blocks, crankshafts, and suspension components.
- Power Generation: To inspect turbine blades, generator rotors, boiler tubes and other components in power plants.
- Construction: To inspect steel structures, bridges, pipelines and other structures.
Benefits of Magnetic Particle Inspection:
1. High Sensitivity
MPI is a highly sensitive inspection technique that detects a wide range of defects, including cracks, porosity, and inclusions, with exceptional accuracy. It can even detect defects too small to be seen with the naked eye, such as fatigue cracks and stress corrosion cracking.
2. Versatility
Magnetic Particle Inspection is a versatile testing method that can be applied to various ferromagnetic materials of different shapes and sizes. This technique can be used to inspect various components, from small parts to large structures.
3. Real-Time Inspection
MPI is a straightforward method that gives rapid results. This allows you to make timely decisions and take corrective actions promptly. You can also employ this testing method to inspect components manufactured or repaired to reduce the risk of supplying defective parts to customers.
4. Cost-Effectiveness
Magnetic Particle Inspection helps to identify and address defects early on, thus preventing costly failures and downtime. Employing this inspection method can also reduce the cost of repairs and replacements.
5. Quick and Portable
The equipment used in MPI is portable and can be easily transported to any inspection site. This makes MPI a convenient and cost-effective option for inspecting components.
How We at Gammax Independent Inspection Services Can Help
Here at Gammax, our skilled technicians have years of experience and expertise. We offer:
1. Comprehensive Inspection
We provide magnetic particle inspection services that meet the diverse requirements of clients from different sectors. Our services range from standard to specialised MPI techniques, but we can also offer personalised inspection solutions if you have a particular need.
2. Advanced Techniques
We use the best contemporary equipment and techniques to ensure you receive precise and dependable results. Our technicians have been trained in the latest inspection techniques, such as alternating current field magnetisation, direct current field magnetisation and pulsed DC magnetisation. Besides, we use the most advanced data analysis tools to interpret inspection results and detect potential defects precisely.
3. Strict Adherence to Standards
We have BS EN ISO 9712-certified professionals and conduct our services according to industry-approved standards and codes. Our team also undergoes an intensive quality control programme, ensuring the inspection results are accurate and reliable.
4. Customised Solutions
We can modify our services to fit the specific needs of each client. We will work with you and craft a customised inspection plan that meets your unique demands. Moreover, we can provide training and technical support that will enable you to better understand the merits of magnetic particle inspection and interpret the inspection results.
5. Prompt and Efficient Service
Our clients depend on our services to keep their operations running smoothly, so we send you the inspection reports and recommendations on time.
Trust Gammax Independent Inspection Services Ltd. for Magnetic Particle Inspection
Irrespective of your sector, choose our trained NDT (Non-destructive testing) experts to offer high-quality Magnetic Particle Inspection services in the UK. Please contact us today to learn more about our MPI services or schedule an inspection.
Our Services
We test welds so that you don’t have to
- GIIS Ltd, Units 12-13, Oaklands Business Park, Bury St Edmunds, Suffolk, IP33 2RW
- 01284 850 888
- info@gammax.co.uk