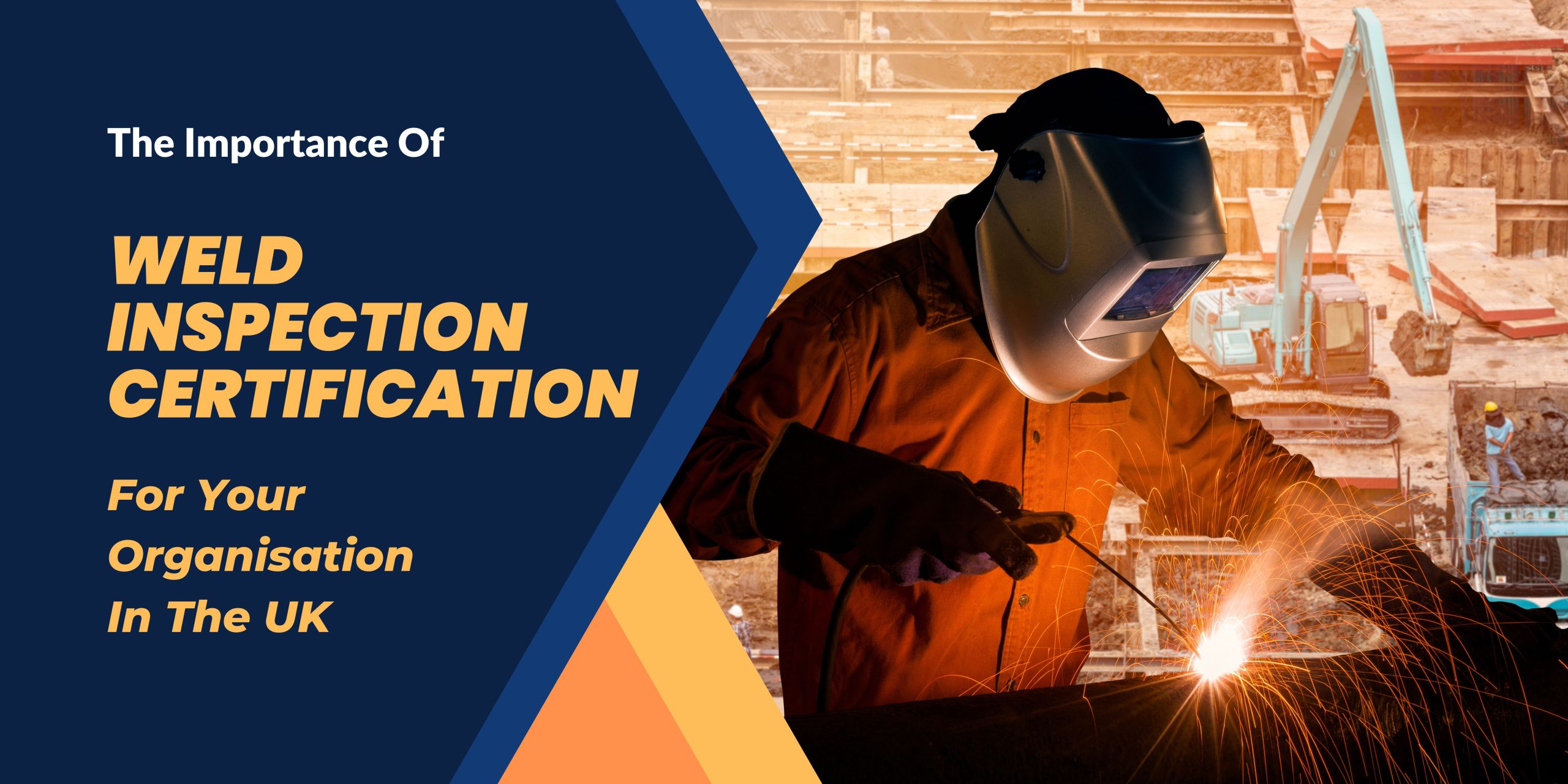
In today’s rapidly evolving industrial landscape, ensuring the quality and integrity of welded structures is paramount for safety. Weld inspection certificates play a pivotal role in upholding these standards, offering organisations in the UK a competitive edge. This blog delves into the significance of gaining a weld inspection certification and how it can positively impact your organisation.
Why Should Your Organisation Gain a Weld Inspection Certification in the UK?
A weld inspection certificate grants your organisation many benefits, some of which are listed below:
1. A Mark of Quality
In welding, precision and quality are uncompromisable. Acquiring a weld inspection certification serves as a testament to your organisation’s dedication to upholding the highest standards of quality. By complying with various inspection protocols, you visibly demonstrate your commitment to crafting welds that possess structural integrity and resilience.
This assurance resonates profoundly with your clients, nurturing a sense of trust. It also prevents potential pitfalls, potentially leading to burdensome rework and expensive repairs in the future.
2. Minimised Liability and Legal Risks
Welding defects or failures can lead to severe accidents, injuries, and even fatalities. Holding a weld inspection certification demonstrates your organisation’s commitment to safety and can significantly reduce liability and legal risks.
In case of any unfortunate incidents, the certification shows your organisation took all necessary precautions to prevent such occurrences, shielding you from the most damaging legal consequences.
3. Compliance With Regulatory Standards
The UK has stringent regulations and standards governing welding practices, particularly in industries like construction, manufacturing, and energy. Gaining a weld inspection certification ensures that your organisation complies with these regulations. This compliance prevents legal hassles and potential fines and demonstrates your social responsibility by prioritising the safety of your workers and the public.
4. Enhanced Reputation and Credibility
In today’s interconnected world, reputation is everything. Holding a weld inspection certification instantly sets your organisation apart from the competition. It signals to potential clients and partners that you are a reliable and trustworthy choice for their welding needs. Your certification becomes a valuable marketing tool, showcasing your commitment to excellence and giving you a competitive advantage in the market.
5. Skilled Workforce and Professional Development
Obtaining a weld inspection certification requires comprehensive training and education for your workforce. This enhances their skill set and fosters a culture of continuous learning and improvement.
A certified team is equipped to handle complex welding tasks with precision, reducing the likelihood of errors and promoting a safer working environment. Additionally, this investment in professional development boosts employee morale, improving customer satisfaction.
6. Cost Savings in The Long Run
While gaining a weld inspection certification requires an initial investment, it offers substantial savings in the long term. Adhering to strict quality control measures minimises the chances of defects or faults in welded structures.
This, in turn, reduces the need for expensive repairs, rework, and potential legal consequences. The certification essentially acts as an insurance policy against financial setbacks caused by subpar welds.
7. Continuous Improvement and Innovation
Earning a weld inspection certification encourages a culture of continuous improvement and innovation within your organisation. As your team strives to meet the stringent certification requirements, they’ll be motivated to explore new techniques, materials, and technologies.
This commitment to staying updated with the latest advancements in the field can lead to increased efficiency, reduced production times, and innovative solutions that set your organisation apart.
8. Global Recognition and Market Expansion
Weld inspection certifications often hold international recognition, allowing your organisation to tap into global markets. The UK’s reputation for quality and safety standards can become a selling point when expanding beyond national borders.
With the certification in hand, you can confidently approach international clients and partners, knowing that your welding processes adhere to rigorous, world-respected standards.
9. Client Confidence and Long-Term Relationships
Clients are more likely to choose a certified welding provider due to the assurance of quality and safety. When you hold a weld inspection certification, you can build strong, long-lasting relationships with your clients based on trust and transparency.
Satisfied clients are more inclined to return for future projects and recommend your services to others. This helps to effectively expand your client base through positive word-of-mouth.
10. Access To Specialised Projects
Certain projects, especially in industries with stringent welding requirements like aerospace or nuclear energy, demand certified welders and inspection processes.
Gaining a weld inspection certification opens doors for your organisation to these specialised and lucrative projects that might otherwise be inaccessible. These projects often come with higher profitability and the chance to showcase your organisation’s capabilities on a larger stage.
11. Environmental Responsibility
Welding processes can have environmental impacts, such as emissions and waste generation. Some certifications emphasise environmentally friendly practices, prompting your organisation to adopt greener welding techniques and reduce its carbon footprint.
This aligns with growing societal expectations for sustainable and eco-friendly practices, making your organisation a responsible player in the industry.
The 3 Stages of Weld Inspection
Proper inspection is crucial throughout the welding process, which means it has to be employed for all three stages—before the weld, during the weld and after the weld. This approach helps to ensure that correct welding techniques are being followed in each step, which is crucial for obtaining a weld inspection certification in the UK. Below we have mentioned how it is carried out for each step:
1. Pre-Weld Inspection
Weld inspection begins with pre-weld inspections that occur before any welding begins. This process involves verifying that all safety protocols are in place, reviewing relevant documentation such as welding procedure specifications (WPS) and ensuring that all necessary materials and tools are prepared. A pre-weld inspection helps to identify potential issues early on, thus, results in a successful welding operation.
2. During-Weld Inspection
During-weld inspection involves monitoring the welding process itself. In this phase heat input is tracked, cleanliness between weld passes is maintained, welding techniques are observed and joint positioning is evaluated to maintain quality. It is one of the most crucial steps in weld inspection. Here the welding process is actively inspected to detect and address problems as they arise to reduce the risk of defects in the finished product.
3. After-Weld Inspection
After-weld inspection is conducted once the weld has cooled and solidified. This step involves checking the weld size, identifying discontinuities or flaws and checking the strength of the weld through various means as well as ensuring that the weld meets all specifications. After-weld inspection is necessary for ensuring the quality of the final product.
Once these inspections are completed without any error, a weld inspection certification is issued.
Types of Weld Inspection
Weld inspections can be categorised into two main types: destructive and non-destructive. Let us take a look at what these two inspection types are along with the methods involved.
Destructive Weld Inspections
Destructive weld inspection (DT) involves evaluating welded joints by intentionally damaging or breaking them to assess their integrity and mechanical properties. This method is essential in critical applications where understanding a weld’s characteristics is paramount for safety and reliability. While effective for detailed assessments, destructive testing can lead to material waste and increased costs due to the destruction of test specimens.
Common Methods of Destructive Weld Inspection:
1. Macro Etch Test: This type of destructive testing involves taking small samples from the weld and subjecting them to an acid etch to reveal internal structures.
2. Fillet Weld Break Test: In fillet weld break, a sample is broken to examine its entire length for defects such as lack of fusion.
3. Transverse Tension Test: Here samples are pulled until failure to determine tensile strength.
4. Guided Bend Test: In guided bend test, samples are bent around a specified radius to evaluate ductility and identify flaws.
Non-Destructive Weld Inspections
Non-destructive weld inspection (NDT) encompasses various techniques that evaluate the quality and integrity of welded joints without employing any destructive procedure. This approach is vital across numerous industries—including aerospace, automotive, oil and gas—where maintaining operational reliability is crucial. NDT allows for thorough evaluations while preserving the integrity of components.
Common NDT Methods:
Visual Inspection (VT): This is the simplest form of NDT where welds are visually examined for surface defects.
Liquid Penetrant Testing (PT): Liquid penetrant testing or dye penetrant testing uses a liquid dye to reveal surface cracks.
Magnetic Particle Testing (MT): In magnetic particle testing a magnetic field is applied to detect surface defects in ferromagnetic materials.
Ultrasonic Testing (UT): This non-destructive testing technique employs high-frequency sound waves to detect internal flaws.
Radiographic Testing (RT): In radiographic testing X-rays or gamma rays are used to produce images revealing internal structures.
Eddy Current Testing (ECT): This NDT method uses electromagnetic induction to identify surface flaws in conductive materials.
Now that we know the types of weld testing, let us take a look at what makes non-destructive weld inspection a preferred choice over destructive welding inspection.
What Makes Non-Destructive Weld Inspection Better than Destructive Weld Inspection
Using non-destructive testing for obtaining weld inspection certification offers several advantages over destructive methods, for example:
Preservation of Assets
One of the most significant advantages of NDT is its ability to preserve the inspected components. Unlike destructive testing, which damages or destroys test specimens, using NDT ensures that materials remain intact and functional after inspection. This preservation is particularly crucial for high-value items, such as aircraft parts or critical infrastructure, where operational continuity is vital.
Cost-Effectiveness
NDT proves to be more cost-effective method for obtaining weld inspection certification. Since it eliminates the need for replacing or repairing the damaged specimens, companies can save significantly on material costs. NDT also allows for early detection of defects, which helps to prevent more serious issues from developing. This saves companies significant amount of money by avoiding downtime and repairs.
Increased Safety
NDT methods ensure enhanced safety as they do not expose materials to potentially destructive forces. This is particularly important for high-stress components where failure could result in catastrophic consequences. By identifying potential issues before they escalate, NDT contributes to a safer working environment and reduces the risk of accidents.
Time Efficiency
NDT methods are typically faster than destructive testing methods, which can expedite the process time for weld inspection certification. Many NDT techniques can be performed on-site and in real-time, allowing for immediate decision-making and reducing operational downtime. This efficiency is especially beneficial in industries with tight production schedules.
Non-Invasiveness
NDT techniques are non-invasive, which means they do not alter the physical properties of the material being tested. This characteristic is crucial for assessing the structural integrity of critical components, as even minor alterations can affect performance. NDT’s ability to conduct inspections without dismantling equipment ensures that operations can continue smoothly.
Continuous Monitoring
NDT allows for ongoing monitoring and routine inspections, enabling early detection of defects or damage throughout the lifecycle of equipment and structures. This proactive approach can prevent unexpected failures and enhance reliability.
Conclusion
The decision to pursue a weld inspection certification in the UK goes beyond just compliance; it’s a strategic investment in your organisation’s future. From fostering innovation and expanding your market reach to minimising risks and promoting environmental responsibility, the benefits are numerous. With a weld inspection certificate, your organisation gains a competitive edge in terms of quality and the opportunities it can seize and the impact it can create.
If you are looking for certified weld inspectors in the UK, at Gammax we provide the best standard of weld inspection. We specialise in all four types of welding procedures – MAG welding, TIG welding, MMA or stick welding and flux-cored arc welding. Our experts can help you choose the right diameter and thickness for pipes and plates to achieve the widest possible qualification range.
All our welding procedures are written using Welding Qualifier software (developed by The Welding Institute) under UKAS accreditation to ISO 17020. Visit our website today to learn more about our various non-destructive inspection processes.
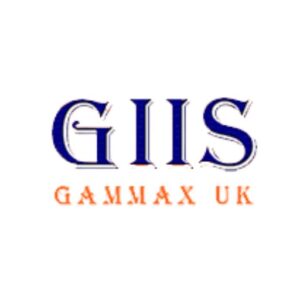
Gammax Team
Here at Gammax Independed Inspection Services, our editorial team consists of BS EN ISO 9712 certified welding experts and consultants. We are committed to offer you latest industry news and up to date information regarding various non destructive inspection procedures.