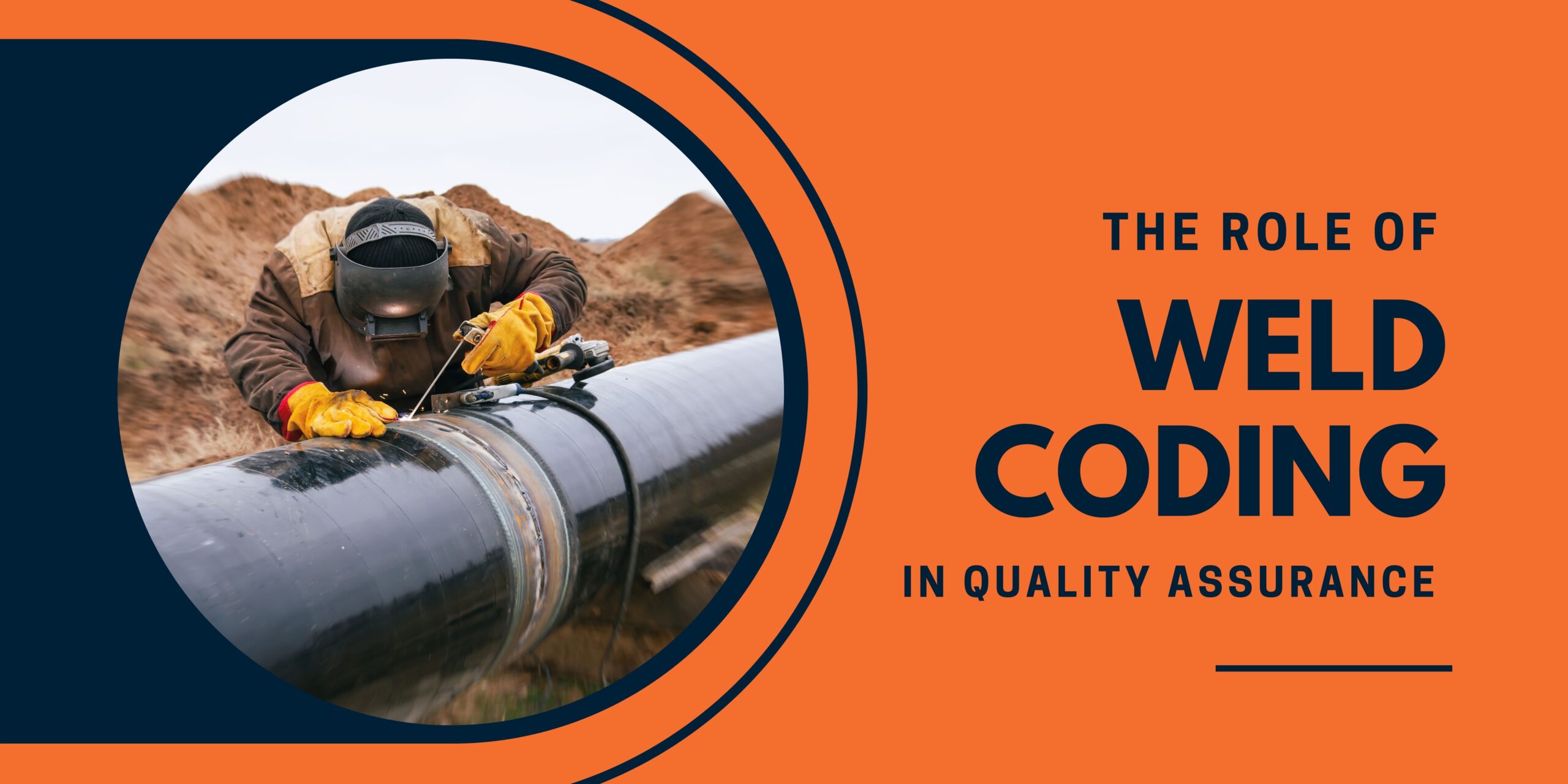
In the welding industry, precision and consistency are paramount. One of the key tools that helps you ensure the integrity of these crucial factors is weld coding. In this blog, we will discuss the role of weld coding in quality assurance, explaining its importance, benefits, and how it helps you maintain high standards in welding processes.
Understanding Weld Coding
This is a systematic method used for labelling and documenting welds in a standardised way. It is often based on industry-specific coding systems, such as ASME or ISO codes. The coding systems use a combination of symbols, numbers, and letters to represent essential information about each weld.
A typical weld code includes information about the type of weld (e.g., fillet weld or butt weld), the welding process used (e.g., TIG or MIG), the welder’s identification, and the specific materials and parameters used in the welding process. This detailed coding process gives a comprehensive picture of each weld’s characteristics.
Role Of Weld Coding:
1. Ensuring Precision
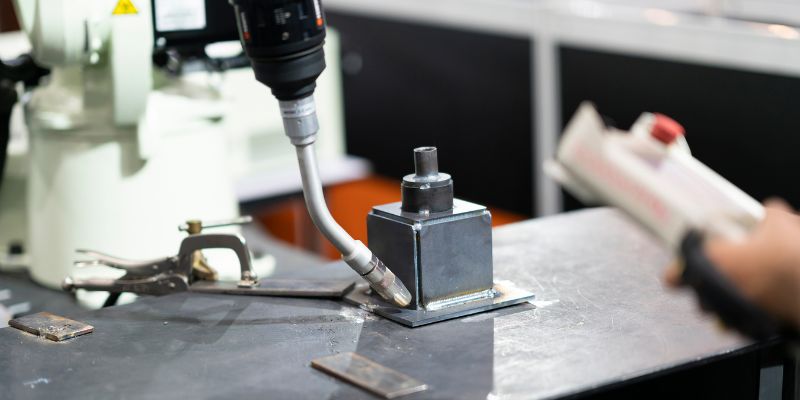
Precision is crucial in welding for achieving the desired strength and integrity in the final product. Weld coding plays a pivotal role in ensuring this precision, as it provides a clear and standardised way of identifying and categorising your welds. This standardisation minimises the chances of errors and deviations during the welding process.
When your welding project has numerous welders working on various components, this coding helps them maintain consistent welding quality across the entire project. Your welders can refer to the codes to ensure they follow the same procedures and use the same materials throughout the project. This reduces the chances of inconsistency in the welds.
2. Quality Control and Documentation
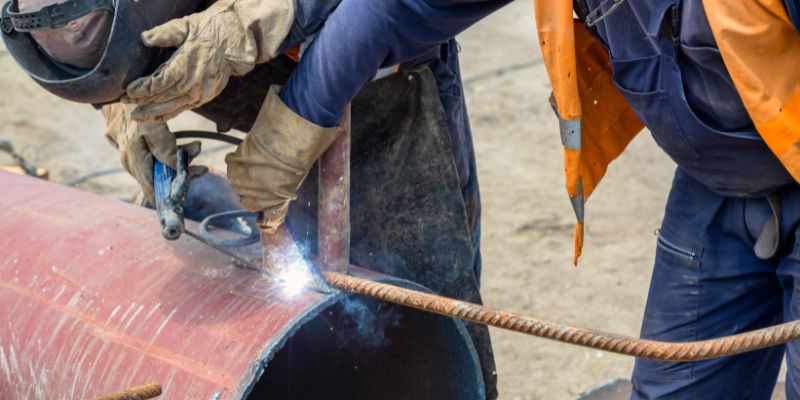
Quality assurance in welding goes beyond producing high-quality welds. It also involves comprehensive documentation of the welding processes. Weld coding acts as a bridge between the welding process and quality control by facilitating documentation. Welders, inspectors, and engineers use these codes to track the progress of your welding project. They identify each weld, cross-reference it with your design specifications, and record details such as welding parameters, inspection results, and any necessary repairs or modifications that maybe required. This documentation not only ensures the adherence of your welding project to quality standards but also serves as a valuable reference for future maintenance or inspection.
3. Efficient Inspection
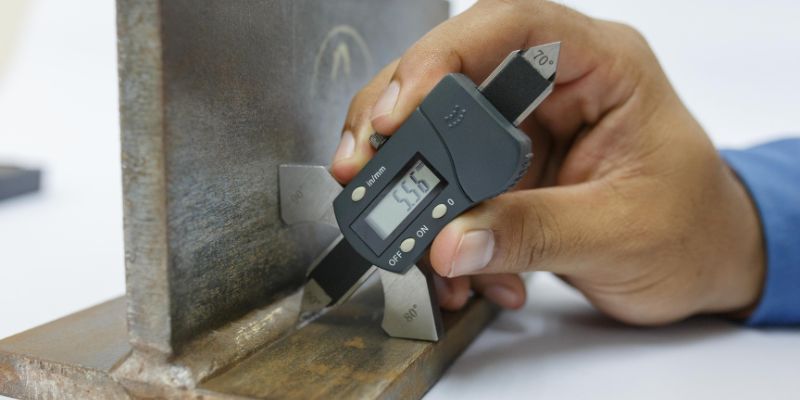
Effective quality assurance involves thorough inspections of your welds to verify their integrity and compliance with specifications. Weld coding simplifies this process by providing inspectors with a clear roadmap. They can quickly refer to the codes to determine the type of weld, acceptable tolerances, and appropriate inspection methods. This efficiency reduces inspection time and ensures that no critical details are overlooked, contributing to a higher level of quality control for your project.
4. Facilitating Communication
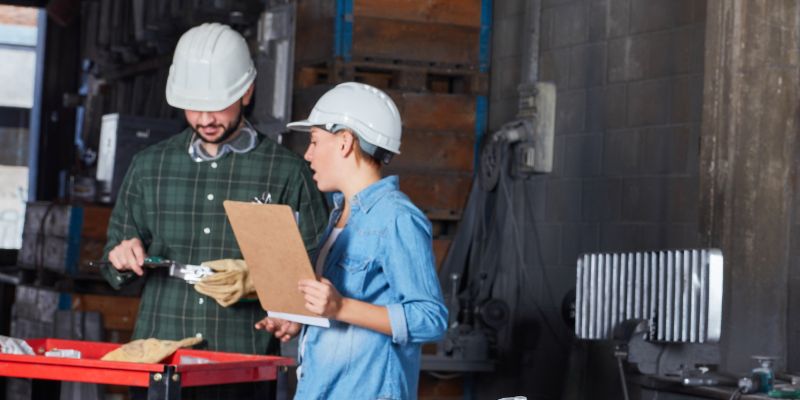
Welding codes serve as a universal language within the welding industry. It enables clear and effective communication among all those involved in your welding project, including welders, inspectors, engineers, and project managers. Wherever a welder needs to communicate a specific welding requirement to an inspector, they can simply refer to the weld code associated with that weld. This ensures that everyone involved understands the welding requirements and standards, which leads to better collaboration and fewer misunderstandings.
5. Meeting Regulatory Standards
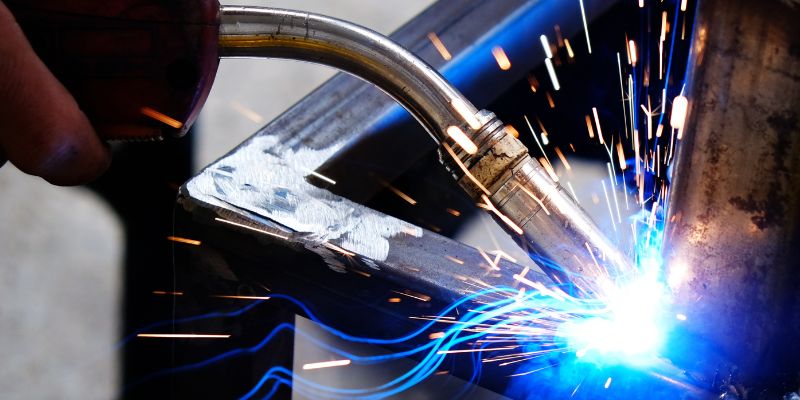
Compliance with industry standards and regulations is paramount for welding projects, especially in sectors like aerospace, automotive, and construction. Weld coding helps you achieve this compliance by providing you with a standardised way to document and verify welds.
For example, the industry you are in may have specific welding codes and standards that must be followed to ensure safety and quality. Weld coding ensures that each weld is recorded in a format that aligns with these regulations, making it easier for your project to pass audits and obtain certifications. This level of compliance is not only necessary for legal requirements; it also showcases your professionalism and commitment to high quality standards within the welding industry.
Conclusion
Weld coding is not merely a formality in welding processes but is a critical tool that ensures precision, documentation, efficient inspection, clear communication, and compliance with regulatory standards. Its role in quality assurance is indispensable, as it enhances the quality of your welds and contributes to the overall success of your welding project. By incorporating weld coding into your welding processes, you can achieve consistent and superior quality in every weld, meeting both industry standards and your client’s expectations.
If you are looking for qualified and experienced welders to help you with weld coding, we are your go-to partner at Gammax. We have been in the field since 1995, and we work under UKAS accreditation in accordance with ISO 17020. All our welders are qualified to BS EN ISO 9606 and ASME IX Codes and use a library of current ASME, ASTM and BS EN standards for interpreting various codes. Visit our website to learn more about our various welding procedure qualifications.
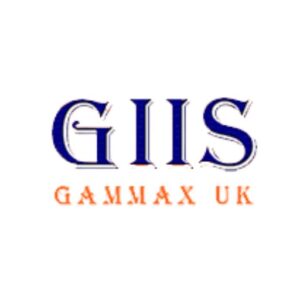
Gammax Team
Here at Gammax Independed Inspection Services, our editorial team consists of BS EN ISO 9712 certified welding experts and consultants. We are committed to offer you latest industry news and up to date information regarding various non destructive inspection procedures.